Was die Stillstandszeit von Maschinen kostet und wie man sie vermeidet
Fallen Maschinen ungeplant aus, erleiden Unternehmen massive finanzielle Verluste. Allerdings wissen viele Hersteller gar nicht, welchen Preis genau sie für Ausfälle zahlen. Wir zeigen, wie hoch die Kosten für die Stillstandszeit von Maschinen sind und wie Sie teure Leerlaufphasen in der Produktion vermeiden.
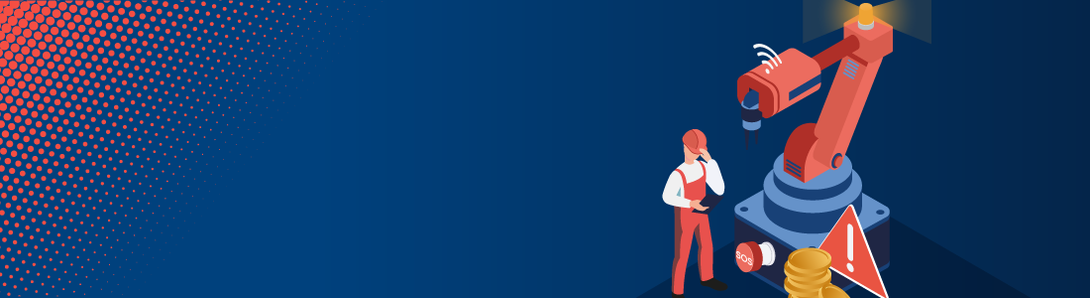
Was sind Stillstandszeiten?
Bei Betreibern gibt es geplante und ungeplante Stillstände. Beide verursachen Kosten. Allerdings lassen sich geplante Pausen, in denen Maschinen und Anlagen gewartet werden, budgetschonend eintakten. Anders als ungeplante Stillstände: In diesen Zeiten fallen Maschinen und Anlagen ohne Vorwarnung aus – und damit auch die Produktion und der Umsatz.
Eine ungeplante Stillstandszeit kann verschiedene Auslöser haben:
- unzureichende Transparenz über Maschinenzustände und damit unerkannter Verschleiß
- ineffizient geplante Service-Einsätze
- mangelhafte Instandhaltung aufgrund von Wissenslücken oder fehlenden Tools
- menschliche Fehler fehlender Schulungen für das Personal
- defekte, fehlende oder falsche Ersatzteile
Produzierende Unternehmen sollten den Ursachen ihrer Maschinenstillstände dringend auf den Grund gehen. Denn Stillstandszeiten bedrohen nicht nur den Umsatz: Um eine Maschine wieder zum Laufen zu bringen, müssen Unternehmen Zeit und Geld in die Reparatur investieren und sind weniger produktiv.
Wie berechnet man Kosten für Stillstände?
Geplante und ungeplante Stillstände können Unternehmen bis zu zehn Prozent ihrer verfügbaren Produktionszeit kosten. Diese Zeit und das Geld, das Hersteller in die Fehlerbehebung investieren müssen, sind unwiederbringlich verloren.
Doch wissen Sie, was eine Stillstandszeit von einer Stunde bei Ihren Maschinen kostet? Wenn nicht, sind Sie in bester Gesellschaft: Laut der International Society of Automation (ISA) geht es 80 Prozent der Unternehmen genauso.
Denn was Produktionsverantwortliche oft nicht bedenken: Neben den direkten Kosten, also dem Umsatzverlust, gehören zu den Stillstandskosten eine Reihe versteckter Kosten. Folgende indirekte Kosten sind der Grund dafür, dass Maschinenstillstände finanziell so schmerzhaft sind:
- Es entstehen ungeplante Kosten für Wartungsarbeiten durch externe Servicetechniker und für Ressourcen zur Fehlerbeseitigung.
- Die Produktionskapazität ist nicht voll ausgelastet, trotzdem fallen während des Stillstands Fixkosten etwa für Löhne oder Betriebsmittel an – das schmälert die Gewinnmarge.
- Während eines Ausfalls gehen Verkaufschancen verloren oder Kunden müssen länger auf ihre Ware warten.
- In der Lebensmittelindustrie kann ein Maschinenausfall den Verlust von Material bedeuten, wenn verderbliche Waren verarbeitet werden.
- Die Reparatur und der Neustart von Maschinen verursachen teure Überstunden.
- In Stillstandszeiten müssen Mitarbeiter ihre Kraft in das Lösen des Problems stecken, wodurch die Produktivität sinkt. Die ISA geht von fünf bis 20 Prozent Produktivitätsverlust aus.
- Ausfälle in der Produktion treffen auch Maschinen- und Anlagenbauer: Die Stillstände ihrer Maschinen kann sich negativ auf ihre Reputation auswirken.
Wie hoch sind die Kosten für Maschinenausfälle?
Was Maschinenausfälle konkret kosten, hat der Predictive-Maintenance-Spezialist Senseye ausgerechnet, der heute zu Siemens gehört:
- Die stündlichen Kosten für Anlagenausfälle übersteigen schnell die 100.000-Dollar-Marke – das sind umgerechnet mehr als 90.000 Euro.
- Insgesamt treten im Schnitt 20 Ausfälle pro Monat und Anlage auf, wodurch 25 Stunden Produktionszeit fehlen.
- Besonders tief müssen große Werke bei Ausfällen in die Tasche greifen: Bei durchschnittlich 323 verlorenen Produktionsstunden entgehen ihnen rund 157 Millionen Euro pro Jahr und Werk.
- Auf die Stunde heruntergebrochen zahlen große Unternehmen circa 490.000 Euro für Umsatzausfälle, Maschinenneustarts und Reparaturen.
- Insgesamt entgehen den Fortune Global 500 Industrieunternehmen durch ungeplante Maschinenstillstände elf Prozent ihres jährlichen Umsatzes – knapp 1.380 Milliarden Euro. Zum Vergleich: Im Bericht von 2021 waren es etwa 797 Milliarden Euro.
So teuer ist ungeplante Stillstandszeit in verschiedenen Industrien
Die Kosten für Maschinenstillstände steigen – und das in einer Zeit, in der Unternehmen durch Krisen und angespannte Finanzmärkte zum Sparen gezwungen sind. Nicht nur große Player sollten deshalb alles daransetzen, ihre Maschinen am Laufen zu halten: Eine höhere Anlagenverfügbarkeit lohnt sich für alle Branchen.
Diese Verluste entstehen durch defekte Maschinen und Anlagen in verschiedenen Industrien:
- Die Kostenspanne bei einer Stunde Stillstand reicht in den untersuchten Branchen von umgerechnet fast 36.000 Euro bei Fast Moving Consumer Goods bis hin zu 1,84 Millionen Euro im Automobilsektor.
- Im Öl- und Gassektor haben sich die Stillstandskosten von 2019 bis 2022 um 50 Prozent verdoppelt auf rund 460.000 Euro.
- Die jährlichen Gesamtkosten für ungeplante Ausfälle in großen Automobilwerken liegen im Schnitt bei je über 550 Millionen Euro.
- In Schwerindustrie, Metallverarbeitung und Bergbau sind es 118 Millionen Euro pro Werk, in der Öl- und Gasbranche rund 137 Millionen Euro.
Übrigens sind Stillstände auch in IT-basierten Branchen kostspielig. So zeigen Zahlen von 2016, dass Ausfälle in Datencentern im Schnitt 8.300 Euro pro Minute kosten.
Auswege aus der Kostenfalle: Wie kann man Stillstandszeiten vermeiden?
Im Kampf gegen Stillstandszeiten ist Wissen Ihre mächtigste Waffe. Der erste Schritt ist, sich der Tragweite und Kosten von Maschinenausfällen bewusst zu werden und zu verstehen, dass Stillstände teuer und Investitionen in notwendige Gegenmaßnahmen gerechtfertigt sind.
Anschließend müssen die Ursachen für Stillstände erkannt und mit routinierter Instandhaltung vermieden werden. Laut Senseye wollen beispielsweise 72 Prozent der Industrieunternehmen ihre Stillstandszeiten mit Predictive Maintenance reduzieren.
Anstatt zu reparieren, wenn es nötig ist, finden Wartungsarbeiten bei präventiver Instandhaltung regelmäßig statt und werden vorausschauend geplant. Dafür ist es wichtig, Servicetechniker mit allen relevanten Maschinen- und Ersatzteilinformationen zu befähigen, Stillstände effizient zu beheben.
Stillstandszeiten von Maschinen reduzieren: So hilft Software dabei
Ob es um die Analyse von Anlagenausfällen und Optimierungspotenzialen oder das Beheben von Maschinendefekten geht – Softwarelösungen bieten Herstellern und Maschinenbetreibern die dafür notwendige Transparenz über Maschinen und Prozesse.
Eine wichtige Rolle spielt der digitale Zwilling. Er bildet den Maschinen- und Anlagenzustand über den gesamten Lebenszyklus ab und verbindet ihn mit Informationen zu abgeschlossenen und geplanten Wartungen, der Technischen Dokumentation und Ersatzteilinformationen.
Digitale Zwillinge wie der Digital Information Twin (DIT) von Quanos sind Voraussetzung für effiziente Serviceeinsätze. Als zentrale Wissensplattform liefert er nicht nur wichtige Informationen für Wartungsaufgaben, sondern bietet intuitive Schritt-für-Schritt-Anleitungen, um Defekte schneller zu beheben.
Da alle notwendigen Informationen vernetzt, digital und in Echtzeit zur Verfügung stehen, können Techniker über mobile Geräte wie Smartphones oder Tablets darauf zugreifen, Reparaturen effizient durchführen. Die Mitarbeiter im Service werden entlastet und können sich schneller wieder anderen Aufgaben widmen.
Erfahren Sie mehr über das effektivste Werkzeug gegen Maschinenstillstände, Quanos InfoTwin, in unserer Produktbroschüre!
Umsatz rauf, Stillstandszeit und Wartungskosten runter
Wer die Kosten von Stillstandszeiten kennt, weiß: Die Investition in Lösungen lohnt sich, wenn sich damit bereits wenige teure Ausfallminuten vermeiden lassen. Mit Strategien wie Predictive Maintenance erzielen Unternehmen laut BearingPoint zum Beispiel 10 Prozent mehr Umsatz und sparen 17 Prozent Wartungs- und Servicekosten.
Zwar lassen sich ungeplante Stillstände nicht vollständig vermeiden. Doch mit der passenden Softwarelösung gelingt es Ihnen, die Verfügbarkeit Ihrer Anlagen signifikant zu erhöhen. Damit schützen Sie Ihr Unternehmen vor Produktionsausfällen und sparen direkte und indirekte Kosten von Maschinenausfällen.
Mit der All-in-One-Lösung von Quanos geben Sie Ihren Servicetechnikern die nötigen Werkzeuge an die Hand, um Fehler schneller beheben zu können. Dazu gehören verständliche Anleitungen, eine übersichtliche Dokumentation und die Möglichkeit, Ersatzteile schnell identifizieren und bestellen zu können.
Andere Artikel von Quanos
Das könnte Sie auch interessieren
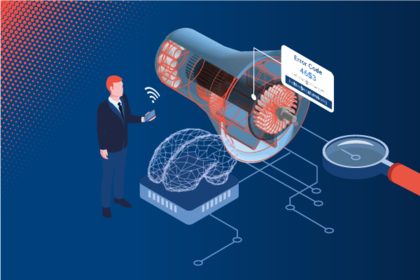
Wartungsmanagement 2.0: Effiziente Instandhaltung im Maschinenbau
In einer Zeit, in der die Maschinenbauindustrie stetig wächst und der Wettbewerb zunimmt, ist es entscheidend, ein ef…
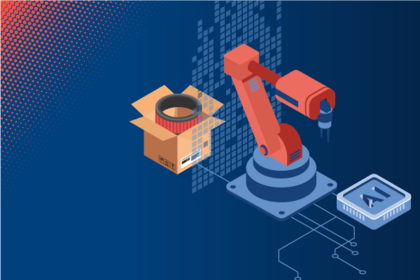
Instandhaltungsmanagement im Maschinenbau: 5 Tipps für maximale Kosteneffizienz
In der heutigen wettbewerbsintensiven Maschinenbauindustrie ist es entscheidend, Instandhaltungsmanagement-Strategien…
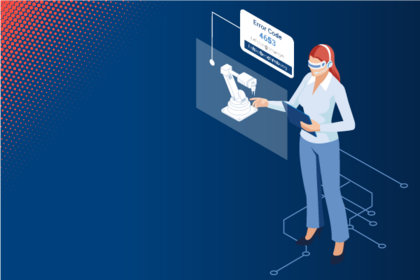
Exzellenter Kundenservice im Maschinenbau: Best Practices für Kundenzufriedenheit und Erfolg
Der Kundenservice spielt eine entscheidende Rolle im Maschinenbau, da er nicht nur zur langfristigen Kundenbindung be…