Maintenance Management 2.0: Efficient Maintenance in Mechanical Engineering
At a time when the mechanical engineering industry is constantly growing and competition is increasing, it is crucial to establish efficient and future-oriented maintenance management. Optimized maintenance management not only helps extend the life of your machines, but can also increase your company's productivity and profitability. In this blog article, you will learn how to revolutionize your maintenance processes for maximum success.
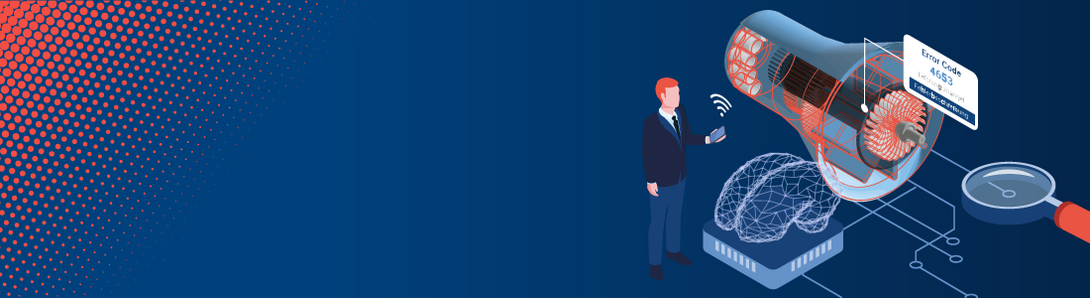
1. Implementation of a condition-based maintenance concept
Traditional, time-based maintenance concepts can be both inefficient and costly. Condition-based maintenance, on the other hand, incorporates the actual condition of a machine into the maintenance process and makes it possible to perform maintenance work exactly when it is needed. Continuous monitoring of machine data and the use of sensors to monitor wear and performance are crucial factors for a condition-based maintenance concept.
2. Taking advantage of the Internet of Things (IoT)
The Internet of Things (IoT) enables machines and equipment to be connected so that important data can be collected and analyzed in real time. By using IoT technologies, you can create more precise maintenance plans by gaining better insight into the condition and performance of your machines. In addition, by analyzing the data collected, you can identify potential problems early and take proactive action to reduce unplanned downtime.
3. Artificial intelligence (AI) and machine learning
Artificial intelligence and machine learning can help make maintenance processes in mechanical engineering even more efficient. By using algorithms that learn from machine data and recognize patterns, you can better plan preventive maintenance measures and make optimal use of resources. This also reduces the total cost of ownership and extends the service life of your machines.
4. Adaptation of spare parts logistics
Optimized spare parts logistics is an important part of efficient maintenance management. Ensure that spare parts are available quickly and easily to minimize unplanned downtime. Use modern logistics solutions and stock critical spare parts in sufficient quantities to be able to react quickly to malfunctions.
5. Training and further education of the maintenance technicians
A well-trained workforce is essential for successful maintenance management. Invest in the further training of your maintenance technicians to ensure that they have the necessary knowledge and skills to effectively maintain modern machines and technologies. Through training and education, you can not only improve the quality of your maintenance services, but also increase employee satisfaction and motivation.
6. Establishing a continuous improvement culture
Efficient maintenance management requires continuous improvement of processes and procedures. Promote a culture of continuous improvement by encouraging your employees to actively participate in identifying improvement potential. Use regular reviews and audits to check the success of your maintenance strategy and make adjustments where necessary.
7. Use mobile solutions and digital tools
Modern mobile solutions and digital tools can significantly increase the efficiency of your maintenance processes. Equip your maintenance technicians with tablets or smartphones to give them access to important information and documentation directly on site. This facilitates communication and enables faster fault diagnosis and rectification. In addition, digital tools such as augmented reality (AR) can help facilitate collaboration between experts and technicians on site.
All information for maintenance in one system
In a modern service information system like Quanos SIS.one, all the relevant information for carrying out maintenance comes together: Spare parts information, 2D and 3D drawings, links to the relevant location in the technical documentation, circuit diagrams, hydraulic plans and much more. Thanks to sophisticated search functions, maintenance technicians save a lot of time when researching information - which ultimately reduces machine downtime. After all, on-site work is completed more quickly when the necessary information is available immediately and in a central location.
Would you like to experience for yourself how easy it is to find the spare parts you need and relevant maintenance information in Quanos SIS.one?