Key info at a glance
- The digital information twin, or DIT for short, integrates product information into a single virtual location and makes it available to the relevant stakeholders.
- The DIT keeps service-relevant data synchronized and up to date.
- A DIT simplifies the work of service technicians, service engineers, aftersales managers, and maintenance staff.
- Digital twins are essential if you want to enjoy the advantages of Industry 4.0 – including predictive maintenance.
- In order to benefit from the digital information twin, manufacturers need corresponding software solutions.
What does digital information twin mean?
”Digital information twin” (DIT) is a buzzword that plant and machinery manufacturers would do well to remember – after all, the future of maintenance, aftersales, and service belongs to it. But what does it actually mean? And what makes the DIT different to a digital twin?
Definition of digital information twin
The DIT is a central platform where technical information and service information about a product, machine, or plant is stored. The data in the DIT are bundled and synchronous, resulting in an integrated information management system that fulfills different functions.
The System:
- Displaying the real status of the product after the sale and in use
- Putting the spotlight on the entire product's life cycle
- Serving as a lifecycle record for a product or machine
- Containing information about spare parts, documentation, and manuals for a certain machine or variant
- Making all the information you need quickly accessible
Distinction from the digital twin
The digital information twin is not to be confused with the digital twin or digital engineering twin. Although both twins represent a virtual model of a real object, they differ in terms of the benefits they offer.
In contrast with the digital engineering twin, the DIT does not simulate any product properties or functions. Instead, it contains comprehensive (service) information. This includes user manuals, service instructions, and spare parts lists. The information is product-specific and stored individually. It reflects the actual configuration of a product or machine.
The intention of a DIT is to provide users with a comprehensive, digital understanding of products, machines, and plant with the help of saved product documents. This makes it a must-have for aftersales & service departments by providing valuable information for targeted and efficient maintenance and service tasks.
The engineering twin enables the real-time exchange of digital information between machines via the IoT. In contrast to this, an information twin provides valuable and varied data for people. This results in a detailed image of a machine, which service technicians and aftersales managers, for instance, can use as a basis to make well-informed decisions.
Who benefits from the DIT?
Those who stand to benefit most from a DIT are manufacturers and operators of machines and plant that have to prepare and supply complex and extensive information about their products. This is because they are currently facing significant challenges:
- High level of manual effort involved in creating and supplying spare parts catalogs and documentation in aftersales & service
- High costs due to incorrect operation or as a result of misidentification of spare parts because relevant information is not universally available
- High workload for IT departments, which delays the introduction of new software solutions
- Strict requirements for the skill level of employees since lots of information is dispersed across different systems such as ERP, CAD, CRM, and PLM
Which goals can companies achieve with a DIT?
- Significant cost savings due to reduced downtime, research time, and waiting times
- More time for core business because there is no need to waste time searching for the necessary information
- Increased customer satisfaction due to a high first time fix rate
- Minimal effort involved in digitalizing service processes
- 24/7-provision of tailored information for partners and customers domestically and internationally
- Better understanding of service figures
- Comprehensive information base for optimizations in aftersales & service
- Basis for developing new, customer-focused services and therefore greater competitiveness
- Improved profitability and higher turnover in aftersales and service through optimized spare parts business
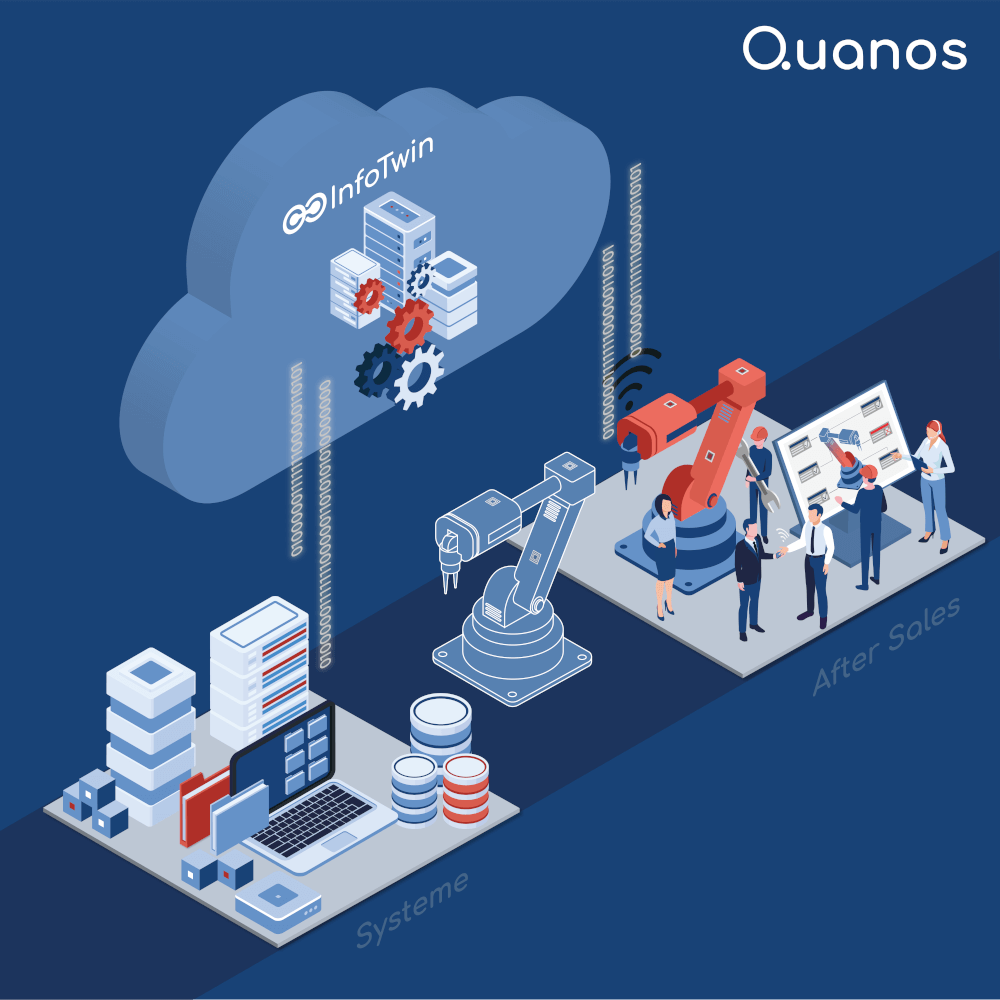
What are the benefits of a digital information twin for aftersales & service?
Service engineers, service technicians, aftersales managers, maintenance staff, and other DIT users no longer have to tediously look for spare parts information and maintenance manuals. Instead, the DIT platform provides an intuitive user interface that makes all the information for their maintenance tasks quickly accessible in digital form.
With a digital information twin, machinery manufacturers generate an intelligent data model of their machines and plant. Not only are data displayed virtually, but they are also prepared and integrated in such a way that creates real added value for the user.
The digital information twin serves as a service information system, which keeps field service engineers informed of changes to work processes. With the help of manuals, it also makes it possible to estimate how long the maintenance work and machine downtime will last.
A digital information twin makes companies fit for the future
The linking of a DIT with artificial intelligence (AI) creates potential for additional benefits in the future:
- AI is able to predict impending component malfunctions, such as the valves in a customer's plant, in good time.
- It also detects that additional valves of the same type and with a similar service life are installed in the plant.
- The system can make suggestions to the service technician and aftersales manager based on this information and offer the customer the corresponding spare parts in advance.
The benefits of a digital information twin at a glance
- Increase the efficiency of their service and maintenance processes, including via predictive maintenance
- Reduce the overall costs of their service and product life cycle management
- Maintain a better overview and a comprehensive understanding of machines, plant, and products
- Boost the exchange of data and insights between their departments
In terms of everyday working life in aftersales & service, the DIT offers the following benefits:
-
Efficient data management: If documentation needs to be adjusted, this can be updated as a package and downloaded automatically to all machine locations.
-
Efficient fleet management: For companies that offer services for vehicle fleets, central data access at fleet level reduces the effort involved in manual data capture, in turn boosting mobility and enabling automated reporting.
-
Lower maintenance costs: Remote maintenance and predictive maintenance enable forward planning of service capacities and reduce travel costs for service personnel.
-
Higher reliability: The more forward-looking and precise planning of maintenance and servicing can be, the faster machines and plant can be put into operation again, reducing non-scheduled downtime.
-
Fewer repairs: 24/7 remote maintenance reduces the number of essential repairs and gives service experts more time to offer their customers first-class service and help them to achieve better results.
How do companies use the digital information twin?
Prerequisites for using a DIT include one platform as a “core infrastructure”, in other words as a single source of truth, for all service data and connected applications. These so-called capabilities comprise tools that can be used to create, manage, and exploit data and connections. For plant and machinery manufacturers, these include documentation systems, spare parts catalog generators, online stores, and customer platforms.
With the right software, companies can secure high Digital Twin performance. They can lay the foundations for this today by digitalizing their processes and aggregating service-relevant information into a central system.
The foundations for a digital information twin
- Integrated data processing
- Consistent master data
- Comprehensive data structures and sufficiently large quantities of data
- Meaningful data models
- Smart integration of all information
- Central system with flexible interfaces for the aggregation of data and information
Quanos Service Solutions offers all the necessary tools to implement a digital information twin. Professional software solutions unlock the potential of technical information and give plant and machinery manufacturers complete control over their content.
What makes a DIT worth using?
Not only does the digital information twin save companies time and money, but it also optimizes their service processes. It is also the solution for the biggest trends in aftersales & service:
- Service digitalization: At every stage of digitalization, plant and machinery manufacturers need the right tools – from digital spare parts catalogs right through to the digital information twin. As a result, complete service digitalization is possible only with a DIT.
- Service 4.0: The evolution from analog service towards Service 4.0 demands digital business models. The sale of machines and plant is moving into the background – the focus is now on their performance. With the digital information twin, machinery manufacturers can guarantee the performance of their products.
- Increasing customer expectations: Plant operators are more sensitive to cost than ever – and they expect fast, tailored service. To meet these expectations, support and service employees need an intelligent, digital platform that provides them with the information to do so.
- Digital transformation: The digital revolution poses unique challenges for maintenance and servicing. The IoT provides valuable data for optimized service – however, these first need to be centrally bundled and evaluated. The digital information twin makes light work of this task.
- Demographic change: Society is getting older and older, which also means that companies are losing more and more knowledge. Solutions such as the DIT are required to safeguard the expertise of service experts for subsequent generations of technicians.
Conclusion: Lay the foundations for future success today with the DIT
Plant and machinery manufacturers are prepared for all these developments and more with Quanos – and at every stage of digitalization at that. Quanos offers modular functions which, when used as a bundle, create a 360° solution for all the challenges of a modern service setup. By contrast, individual features take a targeted approach to resolve acute problems in the early stages of the transformation.
It does not matter whether you already use a digital information twin or whether you want to start by digitalizing individual areas of your aftersales operation. Either way, you will receive a future-proof single source of truth that is flexible and upward compatible.
Here is a summary of the benefits offered by Quanos:
- Cost reduction thanks to the automatic import and integration of relevant data
- Time savings upon implementation thanks to the option of using the solution as an SaaS model in the Quanos Cloud
- Easy implementation of service activities as a result of access to all the necessary information
- Find all the information you need in just a few clicks
- High data security thanks to individual access control for individual users