Dead Spots - A Productivity Drain: How Service Technicians Can Work Efficiently Even Without Internet Access
Service technicians take on many roles - repair experts, problem solvers, and troubleshooters supporting plant operators wherever they’re needed. They can usually be found in factories around the world, where they often encounter unfavorable conditions. One particular challenge they face is call-outs to dead spots. In this blog we look at what no access to the Internet means and what can help.
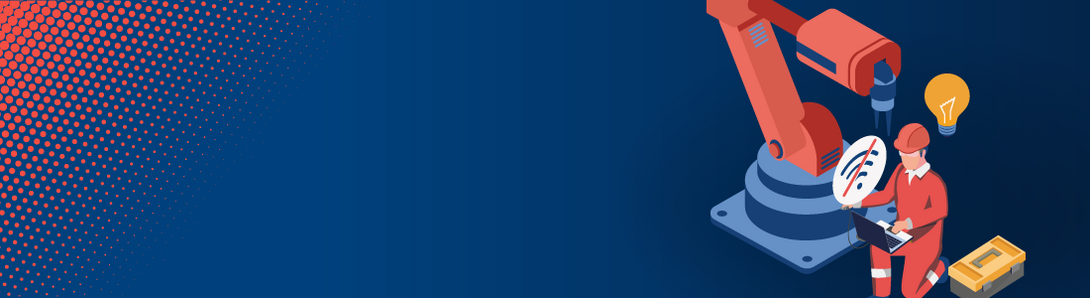
Service technician - the most varied job in the world
While other people travel to and from their home office or company office, service technicians working for machine manufacturers are located wherever the customer needs them. Instead of sitting at a desk, they work on broken-down compressors in production halls, stationary conveyor belts below ground, or frequency converters on the platforms of offshore wind farms.
Alongside their knowledge, the laptop on their lap, tablet in their hand, and smartphone in their pocket are the most important tools field service professionals have at their disposal. Whether in the office, on the way to a service call-out, or at the customer’s premises, these compact aids are how the service technician accesses the employer’s aftersales and service information.
Thanks to digitalization, all the relevant information for the job is just a click or tap away at any time, anywhere. A technician’s smartphone can also be used as a digital camera and direct line to coworkers in the office, making it quick and easy to get help.
But what happens if technicians are alone in protected areas, at remote installations, underground, or out at sea without access to the Internet?
No Internet, no information, no progress
Without Internet access, service technicians’ everyday tasks become a challenge, starting with identifying spare parts. Technicians may usually use service portals or digital spare parts catalogs to find the right parts, but in dead spots they don’t have any up-to-date data available and can’t properly access the technical documentation.
Missing information about spare parts or not being able to clearly identify parts often leads to incorrect orders and service call-outs lasting much longer than planned. If the required parts are available but there is no access to interactive installation instructions, the technician also loses time and the customer is faced with costly downtimes.
One option for getting hold of information despite being in a dead spot is changing location within the plant. If there’s no reception at the machine itself, the technician can go on the lookout for an Internet connection with their smartphone in hand, allowing them to get the information they need and then return to where they were working. However, both their daily step target and the limits of their patience are likely to soon be reached.
If it’s not possible at all to access the Internet, they can still cling to the hope of being able to phone a friend, by trying to reach their coworkers in the office by phone. This is a good way of getting someone else to do the research they aren’t able to do. Of course this involves their colleagues interrupting their own work and, in the worst-case scenario, inadvertently providing the wrong information.
How can service technicians get around the drawbacks of dead spots?
If it’s clear before the call-out that accessing online information could be a challenge, lots of service technicians resort to good preparation and analog workarounds by:
- Taking screenshots of important information from the technical documentation on a smartphone to use later as a memory aid.
- Saving, screenshotting, or taking along a printed copy of information available in PDF format to the customer’s site.
- Making notes so no key information is forgotten.
However, in our fast-paced world, there is a risk that information will already be outdated by the time the technician reaches their destination. A better workaround is for machine and plant manufacturers to make their aftersales and service information available for offline use so service technicians can access it when they’re on call-outs.
What do service technicians actually need without Internet access?
Service technicians need to be able to find information on spare parts and repair instructions even without any Internet access.
Regardless of whether technicians are in dirty and oily environments and regardless of which device they’re using, data from digital sources like spare parts catalogs, service portals, technical documentation, and technician’s digital notes must be...
- usable round-the-clock offline
- the same everywhere
- just as easy to use as in a relaxed office environment
What’s more, clear, quick, and easy navigation through the technical documentation and through spare parts catalogs is important. Many service technicians like to use 3D models or the tree structure of catalogs for this, features that must also be available to them offline and in remote locations, no matter how big the volume of data or cellular network bandwidth where they are.
Accessing relevant information on an app online and offline
There are many ways in which machine manufacturers can support their service technicians on call-outs. Augmented reality and interactive instructions make repairing machines more efficient, 3D spare parts visualization helps them find parts, and digital twins of machines and systems simplify the analysis of faults. However, solutions like these often require a high-speed Internet connection.
Machine and plant manufacturers should also consider their offline colleagues who get their hands dirty during their work but require access to clean data. What these service heroes need are apps that provide seamless offline access to specific content in the aftersales system.
This would make it possible for technicians to work efficiently during their service call-outs, regardless of where they are, the device they’re using, and the data volume, allowing them to save their employer and the customer time and money. Machine manufacturers who already use Quanos InfoTwin to organize their aftersales and service information will in future be able to provide their service technicians with an app for tablets and smartphones that works offline.
Learn more about the Offline Companion App for Quanos InfoTwin in our Fact Sheet: