Demographic Change - Part 2: Conserving Service Knowledge
The "perfect storm in service" - experienced personnel retiring, new personnel being scarce and encountering increasingly complex equipment - requires new ideas and technologies to meet customer demands for reliability and efficiency of equipment and machinery and to provide optimal support for employees. We offer a wide range of intelligent software solutions here.
To preserve as much knowledge as possible and make it accessible, more and more companies are using technical documentation software, in which service instructions, background knowledge, flow charts and everything else can be stored. Supported by images and animations, even less experienced service technicians are able to perform complex maintenance and repair work.
This information is integrated into a modern service information system, which, in addition to the technical documentation, contains a digital spare parts catalog and other content such as schematics, pneumatic and hydraulic diagrams, and intelligently interconnects all the information. The service technician thus receives all information at a glance - in ONE system, anytime and from anywhere. Read Part 1
How do service information systems help your service technicians?
You would like to learn more about how a service information system supports your service technicians in their work?
Then download our brochure on spare part identification now. Download brochure
Maintaining an overview of the current status
The support that software can provide starts with documenting the current status of a plant. An experienced service technician used to know "his" equipment at the customer's site down to the last screw, knew which parts he had replaced, exchanged for different or optimized parts. In the future, service technicians will have to be more flexible and thus be able to service more different systems for more customers. Often, a colleague has performed the last maintenance.
In addition, systems have been in use in many companies for many years - built to a high standard of quality, excellently maintained - and repeatedly retrofitted, modernized, and adapted to new products. As a result, the condition of the equipment in the field deviates more and more from the as-built status that the manufacturers often still have "on the books." Experienced service technicians had the changes in their heads. Today, it is necessary to digitally record these changes so that the preparation of service work can run at the as-installed or as-maintained state.
Efficient service under these conditions is only possible if the changes to the plant are documented and this documentation can be retrieved at any time, from anywhere and by anyone. What is needed is a digital twin - a Digital Information Twin (DIT) - that is identical to the real plant at all times, in which changes made by the service department are stored and maintenance work can be traced.
What is the purpose of a digital twin or Digital Information Twin?
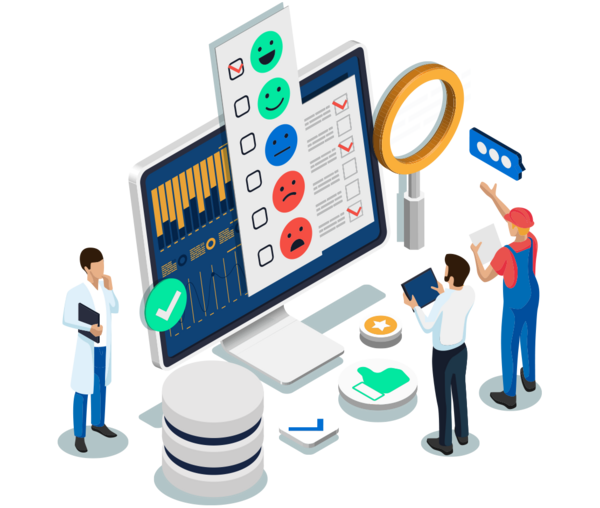
This digital twin stores all available data on the plant that has been generated throughout its lifecycle, from 3D CAD data, bills of materials, service manuals and other documentation to spare parts lists and - in the case of IoT-capable plants - live data from the plant. This makes it possible, for example, to perform installation inspections on the digital model. Thus, before stopping a plant, it is possible to test how a larger component can be removed, which assemblies are in the way and must be dismantled. Finally, it is thus possible to determine the weight of the parts to be moved and thus to plan for the necessary aids such as cranes and forklifts.
But the Digital Information Twin can do even more: if it is fed live data from the plant via the Internet of Things (IoT), it can gather experience and predict potential defects. This time, however, the all-important experience is not stored in the technician's head but in a computer, making it universally usable.
Learn in our Fact Sheet "Bring Knowledge From the Field Into the Service Information System" how you can centrally store experience and valuable knowledge of your service technicians and efficiently document the current condition of your machines:
Keeping experts longer - but sensibly
Keeping employees beyond retirement age - models like this, which often go under the label "senior experts", are being used by more and more companies to avoid losing experienced employees abruptly, but to benefit from their experience for as long as possible. But the relationship between employer and employee is changing dramatically because the vast majority of senior experts don't work for the money, but to remain active and feel needed.
The employer has to do a number of things to make working in retirement attractive to the employee - one possibility is to reduce the amount of travel.
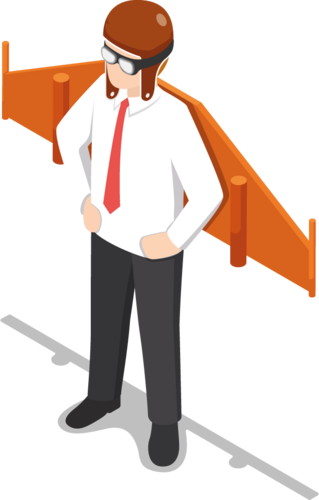
Many service employees are constantly on the road, often around the world, from one customer to the next. As enriching as extensive travel can be at the beginning of a career - at some point, you've gotten to know every airport and long for more peace and quiet. When it comes to being able to deploy experienced service employees after retirement or at the end of their working lives, reducing such travel can be an important building block.
Covid has made it quite clear - many service tasks can also be performed via video conferencing or remote maintenance. Especially the diagnosis of damages is often efficiently possible in cooperation between a local employee of the plant operator and a remotely connected employee of the plant manufacturer. If the expert is not on site, access to complete and up-to-date service information on the plant is more important than ever - the local employee needs as much information as possible and the expert can also work poorly if he does not know the current status of the plant.
In addition, the job profile is fanning out more and more - just like the plant, which is embedded in larger contexts through networking. In the future, the service employee must have a clear understanding of the machine embedded in this overall environment and be able to anticipate what changes to the machine will mean for the process as a whole. Away from being a repairer and problem solver and towards being a process consultant and optimizer.
This enables the service technician to move up the career ladder through further training, to work in larger contexts and, for example, to avoid having to travel a lot. For the company, the advantage is that employees can be promoted in the long term, have a clear career path, and can thus be retained for longer.
Working efficiently - situation- and product-related service information

We all know it from cars - to this day, many of them are delivered with manuals that are inches thick, because these manuals cover all possible engine and equipment variants. The driver must first laboriously search for which parts of the documentation apply to his individual vehicle.
The situation is similar for many plants: Generic documentation that describes all conceivable variants. This is of little concern as long as the documentation plays a minor role, because the service technician knows the system and its peculiarities exactly and has all the important information in his head: He knows which wear and spare parts are needed for this plant and how to replace them.
This changes radically when the experienced employees retire and younger, less experienced employees are expected to perform the maintenance or repair. The more the service technician relies on technical documentation for his work, the more time he wastes searching for the right information in the jumble of irrelevant instructions.
Efficient work in this situation requires access to situation- and product-related service information:
A service information system such as Quanos SIS.one provides the service technician with access to machine- and customer-specific technical documentation, spare parts catalogs, circuit and pneumatic diagrams, and other service-relevant information. He has all the information he needs at a glance to carry out repairs or maintenance efficiently and correctly. He orders the spare parts he needs directly online via the integrated spare parts store.