Digital spare parts portals ensure outstanding service performance at airports
The aviation industry is aiming to become more efficient and more sustainable. The first step will be to resolve maintenance backlogs. Digital platforms help aircraft manufacturers optimize their service processes and thus allow them to focus on other important areas.
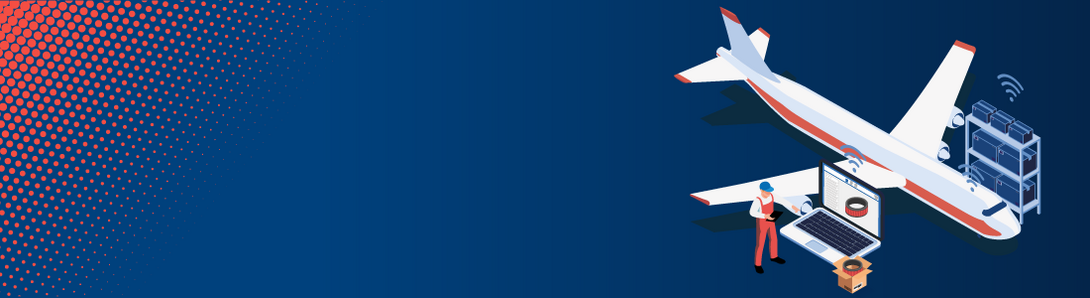
An industry is landing on the ground of hard facts
Aftersales topics such as spare parts have rarely featured as prominently in the media as they did in the summer of 2023. Headlines reported that Russia's airports were running out of spare parts because of the war in Ukraine and that a turbine manufacturer had installed unapproved parts in its turbines because of falsified certificates.
These headlines illustrate the role played by the availability of spare parts at airports. They also clearly show that in cases of problems with aircraft components, it’s important to know exactly which parts are installed where.
Since the Covid-19 crisis, the challenges faced by the aviation industry have been a permanent topic in the media.
- During the pandemic, airport operators and airlines suffered from the global travel freeze. After the global health crisis subsided, climate protests, staff shortages, and rising fuel costs meant that operations were slow to resume.
- One of the major challenges currently facing the aviation industry is the need for climate-neutral flying with environmentally compatible fuels and alternative propulsion systems. However, suitable fuels have to be developed and produced in huge quantities. The aviation industry itself does not currently believe that CO2 -free flying will be possible by 2050.
- A further goal is to achieve greater sustainability on the ground. Airport operators are looking to make operations more efficient, low-cost, climate-friendly, and flexible. But there is a shortage of skilled labor to implement these plans. For example, at Frankfurt Airport there is a shortage of 12,000 employees this year.
- Many of these challenges could be mastered by means of automatization/automation, but the road ahead is long. Unlike the situation in the manufacturing industry, there are fewer recurring processes in the aviation industry that can be easily automated.
In addition, there are some challenges that cut across all industries. Airport operators are having to find strategies to effectively counter the shortage of skilled labor and rising costs.
Reaching the next level of service data and technical documentation with the Digital Information Twin (DIT)
The best way to reduce complexity is to have lean processes and an excellent overview. Through digitization, aircraft manufacturers, airport operators, and other service organizations in the aviation sector can achieve these goals. Well-structured information about spare parts and service, improved spare parts management, and centralized service portals for vehicles and aircraft are the key to greater transparency and efficiency.
If you are also facing these challenges, you need digital tools to overcome them. These not only bring more structure to your service but also provide the foundation for further improvements. For example, software solutions help you network and analyze your data so that you can coordinate maintenance more efficiently. For example, if flight data is evaluated with the help of sensors, the replacement of components can be planned in a more targeted manner.
Quanos InfoTwin — a cloud-based platform that creates a digital twin of your aftersales processes —is the solution for raising your service to the next level. This module-based structure offers users a low-threshold entry into digital workflows. It can be gradually integrated into your processes and connected with your existing IT systems.
Quanos InfoTwin brings your aftersales data, technical documentation, spare parts management, and data from other relevant sources into a single service portal. Whether it's the maintenance of an engine, a transport vehicle or a conveyor belt, service engineers can find all the relevant data they need in one single location, 24/7.
The well-structured overview of spare parts for each machine or vehicle enables you to identify the part you are looking for and significantly reduces the workload of your service team. During maintenance work, Quanos InfoTwin supports technicians with step-by-step guidance and provides additional information about the spare part or its environment on request.
Connected service information in real life
MAFI Transport-Systeme GmbH and its sister company TREPEL Airport Equipment GmbH have benefited from the advantages of a digital service portal for years. These companies offer their customers tailor-made, machine-specific spare parts catalogs that also include the details of machine modifications.
The service portal also provides price information and the expected delivery dates at a glance — a feature that customers are particularly interested in during periods of spare parts shortages and cost constraints.
The aircraft manufacturer Diamond Aircraft is a perfect example of the fact that digital solutions can easily satisfy even the most demanding requirements for technical documentation and flight safety. Aviation companies need to observe detailed official regulations. And aircraft manufacturers are required to provide the necessary technical documentation for inspection, maintenance, and repair.