Digitalization at KAMPF
Digitalization is the word on everyone's lips. And that is exactly where the problem lies. Because it's often difficult to imagine exactly what the effects of digitalization will be. What problems does digitalization solve? What new things does it make possible? KAMPF has been driving forward digitalization in its technical writing and customer service departments. Two managers told us how digitalization has impacted business processes in their company.
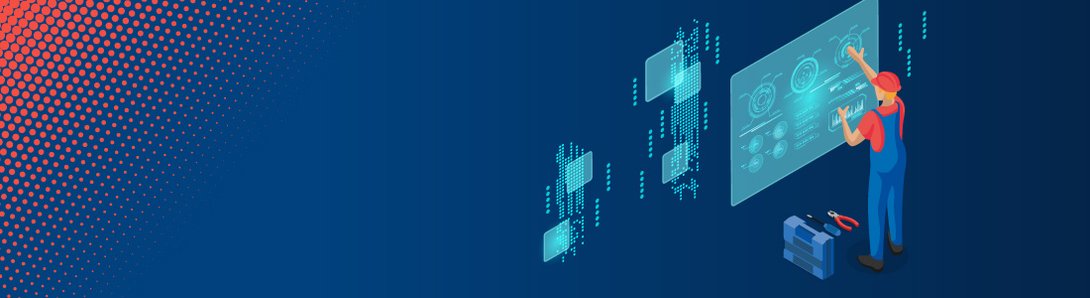
KAMPF – Holistic optimization through digitalization
Anyone that has to wrap or cut papers and foil on an industrial scale knows KAMPF. Based in Wiehl in the German state of North Rhine-Westphalia, KAMPF is a leading expert in the field of cutting and wrapping machines and the largest manufacturer worldwide in this market segment. It has earned this market position through continuous innovation over more than one hundred years. KAMPF's goal is not only to sell machines, but to offer complete solutions that achieve the optimal processing of input material through to the packaged product. KAMPF was therefore an early adopter of digitalization to implement a holistic approach to optimizing production processes.
For Dennis Löhe (Head of Technical Writing) and Patrick Noss (responsible for the KAMPF customer portal in the Digital Customer Solutions department), focusing on seamless digitalization in technical documentation and spare parts management was an obvious choice.
Digitalized technical writing
For the technical writing department at KAMPF, as for so many companies, the starting point was the file-based creation of documentation – in this case with Broadvision Quicksilver. Although the file-based approach made it possible to publish manuals and technical literature as a pdf, it left a lot to be desired.
During a CMS evaluation project in 2016, ST4 was chosen as the tool for the technical writing department: a decision that has since proven to be most inspired. Whereas all design, content creation, and content management tasks had to be carried out by the technical writing department in the previous workflow, the new system provides a lot of flexibility as it 'thinks for itself' and can reduce the workload for authors when it comes to reusing content, translation management, and versioning.
The functionality that enables each content unit in SCHEMA ST4 to be provided with metadata, i.e., information about information, has proven particularly helpful. This allows any content to be classified precisely and prepared for later automatic generation. Not only can ST4 import data from other sources in the company (customer numbers, product data, etc.) as a result, but it can also automatically provide content for other systems. This means, for example, that maintenance information can be exchanged in XML format with the IIOT platform and integrated into a maintenance calendar there. Videos can also be automatically provided with important additional information and the terminology data in ST4 can be exported in the form of a company-wide lexicon. The possibilities are endless as the output formats of SCHEMA ST4 are highly flexible thanks to XML.
From the spare parts catalogue to the customer portal
A very similar development took place in the management of spare parts, which also started with a file-based system. Offline spare parts catalogues were produced here using Excel parts lists and XVL drawings. This changed in 2022 due to the introduction of SIS.One Workbench. As a result, the complete catalogues are now available online in the customer portal.
Even more significantly, the work process for creating catalogues has changed. Previously, information had to be drawn from PDM and ERP in a time-consuming process. Matching parts lists and drawings also took a lot of time. Today, these information processes are largely automated and converge in a coordinated manner in the EPC system, allowing workloads to be significantly reduced. At the same time, the quality of information has been increased and more convenient access to spare parts information for customers has been made possible thanks to the online portal.
What has been achieved so far and what comes next?
Increasing digitalization was clearly the right decision for KAMPF. Not only can a number of processes be automated and made simpler, but the digital exchange between the technical writing, service, and aftersales departments has also added real value, benefitting KAMPF internally as well as the company's customers. This has resulted in an information twin which has been seamlessly integrated into many company services.
The path ahead is already clear. “In the future, we want to focus even more on single source solutions and expand the exchange between third party systems and ST4. For example, the spare parts catalogue and ST4 should also communicate with each other automatically,” explains Dennis Löhe, adding: “Our data is becoming smarter. We are ensuring this by already enriching our data with the right information today, in order to benefit even more from further digitalization tomorrow.”