Technical Writing 4.0: How BERNINA, Bühler, and Miele Are Building Smart Information Structures
Technical writing plays an underestimated role in many companies—with teams often working in isolation and restricted to producing manuals. But in our age of digitization, its potential is being rediscovered. At BERNINA, Bühler, and Miele, technical writing is developing into a central hub that connects departments and builds smart information structures.
In our webinar, Mirko Trepzik (BERNINA), Daniel Ott (Bühler AG), and David Kavermann (Miele) shared their innovative approaches. They explained how they used the idea of a “single source of truth” to break down information silos and create a standardized database that not only increases efficiency but also lays the foundation for digital transformation. In the following, we’ll touch on the most important insights from the webinar once again.
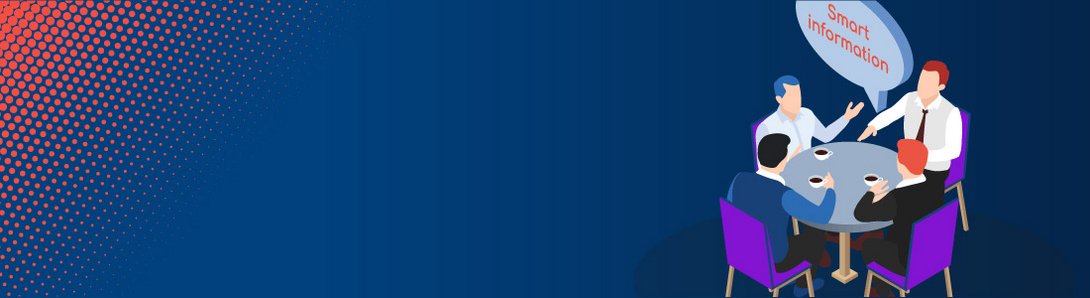
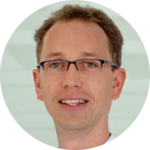
Mr. Trepzik, could you briefly tell us about your role at BERNINA and the vision behind your project?
Mirko Trepzik: Of course! I’ve been working in technical communication for over 20 years and have been with BERNINA, a leading global manufacturer of sewing and embroidery machines, for six years now. Our vision is to establish technical documentation as an information hub within the company. This means that we don’t just write instructions, but collect data from the various departments and prepare them in such a way that they can be distributed to different target groups in small, targeted chunks of information.
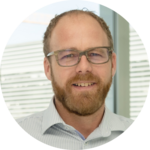
Mr. Ott, can you give us an insight into your work at Bühler?
Daniel Ott: I’d be happy to. I work as a data engineer and project manager in the Advanced Materials division. Bühler is a global machinery and plant constructor with over 12,400 employees. We’ve set ourselves the goal of creating a centralized single source of truth for our technical information in order to avoid redundancies and ensure a consistent information base across all locations.
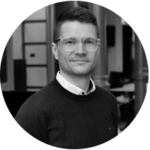
That sounds fascinating. Mr. Kavermann, you also have a clear vision for managing technical information at Miele. Can you briefly explain your approach?
David Kavermann: Of course. At Miele, the focus is on digital transformation and making smart information available. We develop digital user guides and interactive assistance solutions that support our customers exactly when they need it—be it for operating our appliances or providing inspiration on how best to use our products.
To better understand your vision and the objectives behind your projects, I’d like to ask why you decided to embark on these projects?
Mirko Trepzik: Our goal at BERNINA was to build information bridges. Departments often work in isolation from each other, and technical documentation has long been an island unto itself. We wanted to break down the data silos and make sure that all relevant information is brought together in a single data pool by networking it in a more effective way. The idea behind this is that, as technical writers, we not only produce information but also process it for the entire organization as an internal service provider.
In other words, the documentation team isn’t just a reactive service provider anymore but is instead actively integrated into the information flow. Mr. Ott, what was your motivation?
Daniel Ott: We wanted to move away from an unstructured approach in which each site maintains its own sources of information. With around 130 to 180 manuals every year in the Grains & Foods division alone, maintaining an overview proved extremely difficult. A single source of truth was the logical step that would let us enhance efficiency and ensure consistency—it establishes the basis for future developments, such as the digital twin of our machines.
So you were looking to resolve the information overload and redundancies. Mr. Kavermann, what objectives are you pursuing with this approach?
David Kavermann: We recognized that the needs of our customers are very different today than they were a few years ago. We wanted to provide context-specific and interactive information that helps customers exactly when they need it. This was our motivation behind the shift towards digital information management—transforming traditional manuals into digital experiences.
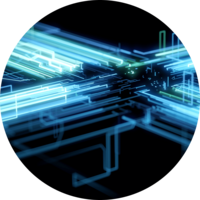
Learn more about smart information!
The path to digital transformation in the machine and plant construction sector is being led by smart information in aftersales & service and technical documentation, as well as software solutions from Quanos. This means that your data will pave the way for your success and facilitate interaction between humans and machines.
You've all described your main objectives, but how exactly did you put these visions into practice?
Mirko Trepzik: We took it step by step. The first phase consisted of optimizing internal processes and building a powerful tool landscape. Then we networked with other departments and began transferring the information from the various areas into a central data pool—a process that required ongoing communication and a clear understanding of what information is generated where and how it can be used.
It sounds like you put a lot of effort into getting things up and running. Mr. Ott, what did the process look like at Bühler?
Daniel Ott: We also proceeded on a step-by-step basis, initially gathering together the requirements of the various departments during small-scale meetings. This resulted in what we named the DICE project (standing for Dynamic Interactive Customer Experience), which is aimed at standardizing the entire tool landscape. We focused on quality data and databases so we could establish a solid foundation for the single source of truth.
Mr. Kavermann, what approach have you adopted at Miele?
David Kavermann: First of all, we analyzed the current situation in detail and used customer questionnaires to get an idea of their information requirements. We then developed scenarios to determine what information is needed when and how it can best be provided. This gave us the basis for moving ahead with the digital transformation of our documentation processes.
It sounds like you’ve achieved a lot already. What steps will you be taking next?
Mirko Trepzik: We now want to scale up the information even further and roll it out to our affiliated companies and branches—in the long term, we want every employee to have access to the information they need at the touch of a button.
Daniel Ott: Our next goal is to fully integrate the single source of truth across the entire product life cycle so that we can automatically generate information for new machines and services.
David Kavermann: We will continue to closely monitor the needs of our customers, and constantly adapt our digital content in order to offer the most personalized user experience possible.
Finally, what tips do you have for companies that are thinking of embarking on similar projects?
Mirko Trepzik: You should definitely start small and build on existing processes. Networks and good change management are the key.
Daniel Ott: Strong backing from the management team is crucial, because without support from the top it’s difficult to implement major change projects. Smart information is an important part of digitization.
David Kavermann: You always have to think in terms of the customer and be prepared to learn from them, because their needs are ultimately the measure of your success.
Many thanks to all three experts for this inspiring discussion
Mirko Trepzik, Information Designer, Content Strategist, Technical Writer, Lead Content Manager @ BERNINA
Mirko Trepzik heads up the Information Design department at BERNINA International AG and likes to think outside the box. He keeps a watchful eye on the company’s single source of truth so it can be rolled out step by step across the company. Mirko is focused on collecting and processing data and creating new information products with the aim of creating added value for customers and the company as a whole.
David Kavermann, Head of Content Management @ Miele
David Kavermann graduated with a BA in Technical Writing and an MSc in Communication & Media Management from Karlsruhe University of Applied Sciences. In 2016, he began his career with Robert Bosch GmbH in the Automotive Aftermarket division as an information developer and architect for technical communication. He has been Information Manager at Miele & Cie. KG since October 2021, where he is responsible for company-wide content management for technical communication.
Daniel Ott, Head of Technical Documentation @ Bühler Group
Daniel Ott has been with the Bühler Group since 2013 and is Head of Digital Product Information for the Grains & Food business unit. His primary task is to create and maintain technical documentation for end customers, while also managing the DICE project, which aims to digitize technical product information. The focal points of the project are standardizing processes and roles, and harmonizing the company’s global IT architecture.