How to Maintain Rotating Machines Effectively
In many plants and industrial processes, rotating machines play an important role and keep the whole show on the road. Careful maintenance is important for ensuring minimal disruption to your business. This article examines the challenges faced by service technicians, and how they can carry out their work as effectively as possible.
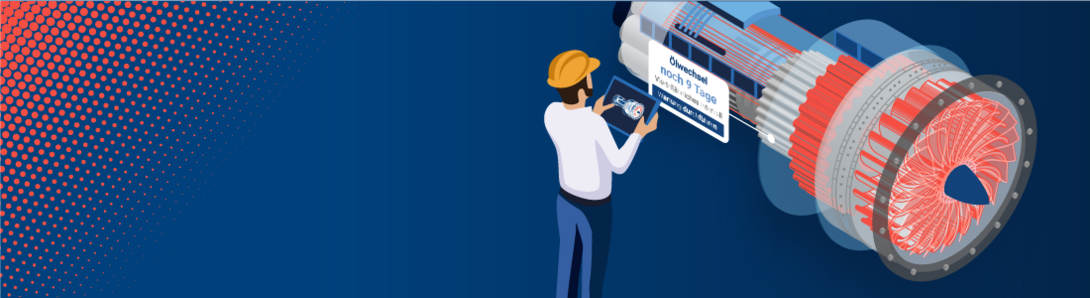
Rotating machines: It’s all about productivity
Without rotating machines, there would be no production: Mechanical devices that produce rotary force drive many important processes in industry. Whether motors, pumps, gears, conveyor belts, turbines or compressors – it is all about generating energy, performing mechanical work, handling materials or powering tools, systems and vehicles.
Due to their diverse capabilities, they can be used in different sectors of industry, such as energy and water management, transportation, or manufacturing. As rotating machines are involved in so many industrial workflows, the productivity of many systems depends on them.
If they are running out of true, efficiency losses will be experienced. If rotating equipment requires repeated repairs or regularly break down, this will usually equate to high financial losses for operators: Production downtime is expensive, and wastes valuable time and resources.
This is why maintaining and servicing rotating machines is of such importance for plant operators. However, it does come with some major challenges for service teams.
Maintaining rotating machines: Timing is everything
There are various reasons rotating components may break down. They are constantly in motion, have to operate in harsh environments at extreme temperature, or come into contact with aggressive substances.
The following are just some of the problems that can necessitate maintenance or repairs:
- Increased friction caused by inadequate or incorrect lubrication speeds up component wear
- Unresolved imbalances cause excessive vibration and lead to structural damage
- Soiling due to dust or oil penetration impairs machine functionality
- Misalignment during installation results in excessive stress on rotating machine components
- Operating faults, especially in motors, quickly lead to overheating and ultimately to breakdown
One of the major challenges when maintaining rotating machines if there is a malfunction is tracing the source of the fault as quickly as possible in order to keep downtime to a minimum.
Service teams need to work out the right time to carry out maintenance. Servicing should not take place too soon, otherwise parts may be replaced unnecessarily, nor should maintenance wait until the damage has already been done.
Equally, technicians must be able to work efficiently and purposefully to ensure time is not lost during maintenance. They therefore need detailed information about the actual problem, and the parts and steps required to rectify it.
For this to happen, service technicians need to keep a close eye on the status of the machines, and require access to all the relevant information for trouble-free maintenance.
Maintaining rotating machines: It’s best to be proactive and well-informed
The best way for manufacturers and operators to maintain rotating machines effectively is using proactive maintenance strategies – such as predictive maintenance.
With this method of maintenance and servicing, rather than maintenance intervals, it is sensors, IoT technologies, and algorithms that dictate when work is carried out on the machines:
- Sensors monitor the status of a machine continuously and in real time by measuring parameters such as temperature, power supply quality, and vibrations, providing valuable information about operation of the machines.
- Using an IIoT interface, data from every single sensor can be consolidated and evaluated in central software.
- With the support of artificial intelligence (AI) and algorithms, service technicians can identify deviations from the normal state of the monitored parameters and are given valuable recommendations for efficient maintenance measures.
If operating problems are looming, the machine automatically indicates that maintenance is required. This has two important benefits:
- Service technicians know exactly what maintenance is required, and which parts need to be replaced.
- Operators then only have to stop their system when maintenance is unavoidable, and there would otherwise be the threat of expensive breakdowns.
Service information enables rotating machines to be repaired efficiently
As well as a sensor-based early warning system, transparent information about the proper maintenance of the affected machine and interactive step-by-step instructions ensure that service technicians can carry out the necessary maintenance steps efficiently.
This requires current data about the machines, the availability of the necessary spare parts and the content of technical documentation to be available centrally and digitally. With the right software, you can make sure that your technicians have at hand all the tools, parts and information required to carry out maintenance efficiently.
Quanos InfoTwin is a cloud-based software solution that combines data from IIoT systems, sensors and technical documentation with service and spare parts information.
A platform for all machines and maintenance tasks
The digital platform for aftersales and service teams makes all relevant information and interactive step-by-step instructions available. It also creates a digital twin of rotating equipment and the entire machine park.
With a digital twin, manufacturers and machine operators can
- lay the foundation for the strategic maintenance of their rotating and all other machines,
- achieve greater efficiency in service and maintenance, and
- reduce expensive downtime.
These are all important requirements not only for saving maintenance costs, but also for predictive maintenance. This helps machine manufacturers take their maintenance strategy to the next level, and offer their customers as-a-service business models, to help them stay competitive in future.
If you want to bring together smart information for the intelligent maintenance of your machines in a single system, get to know Quanos InfoTwin now.