Benefits of an Interactive Spare Parts Catalog within Workforce Management
Not only service technicians know this situation: A customers machine stands still and fast support is needed. However, there is not enough information on hand to ensure a fast solution. Neither descriptive documentation like manuals or repair instructions, nor graphics, photos or 3D models. Even the parts lists are missing to identify the needed spare parts.
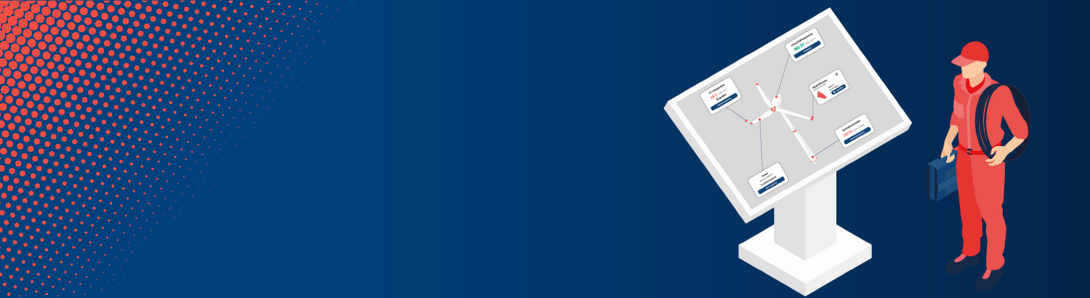
That’s why it is unavoidable to detect the defect part on-site. Additionally, the manufacturers hotline has to be called several times to find out the cause and to order the needed parts. Consequently, a minimum of two trips to the customers site are necessary. That does not only costs time but also money. For the customer and for the manufacturer. But mobileX and Quanos have the solution!
Collaboration offers Mobile Access to Spare Parts Catalogs and optimizes Service Processes
The mobileX AG and Docware GmbH formed an alliance to expand the mobile Worforcemanagement solution mobile-MIP for Field Service with the spare parts catalogue software PARTS-PUBLISHER.
The solution mobileX-MIP for Field Service covers the entire process of service calls. From the commissioning to the finished service report. The interactive spare parts and service information system PARTS-PUBLISHER optimises the supply of spare parts, service and product information.
The integration of PARTS-PUBLISHER in mobileX-MIP for Field Service provides service technicians with mobile devices to gain access to customers’ parts lists, exploded views, photos, 3D models, schematics, prices and descriptive documentation, like manuals, out of different data sources (ERP, PLM, CMS, DMS, CAD systems). As a service technician you may get information about specific machines or assembly groups, enter orders or prepare cost estimates for spare parts.
The combination of mobile access of service technician via mobile-MIP for Field Service and spare parts catalogue software PARTS-PUBLISHER accelerates the ordering process, decreases downtime of plants, provides a higher customer satisfaction and quality and optimises the whole service process.
What is an Interactive Spare Parts Catalog?
An interactive spare parts catalogue contains all data relevant for spare parts identification and ordering in a structured form.
The catalogue …
- comprises amongst other things: linked spare parts, schematics, maintenance, repair, installation, attachment information
- includes illustrations, like pictures, 3D graphics or exploded views
- is an electronically generated catalogue, published via data media (like CD, DVD, USB stick) or communication networks (Internet, intranet).
- contains all relevant data for spare parts identification and ordering
- incorporates a complete linked service documentation, including repair manual and maintenance, as you wish
- controls the access to data through access authorisation and user roles
- can be easily integrated in existing processes and IT systems
Why is an Interactive Spare Parts Catalogue required?
Whether plant or mechanical engineering, vehicle construction, component or equipment manufacturing, the spare parts business became strategically more and more important within the last years. Spare parts are a major revenue driver in service for companies with business in plant and mechanical engineering. That’s why it is not a surprise, that electronic spare parts catalogues and web shops are ranked in the Top 5 of IT-investment projects of mechanical engineering.
Manufacturers track with a huge interest, how the market meets their requirements to offer customers, service technicians or dealers fast support and simplify the purchase order processing. For this reason, electronic spare parts catalogues with web shop connections are applied increasingly.
Companies are often confronted with the following struggles:
- Spare parts and service information is located in different places and systems
- Expertise and know-how of employees is not always available
- Continuous distribution and updating is extremely time-consuming
- Often manual data update, connection to ERP or PDM not continuously
- Spare parts identification is costly and takes a while
- Greater effort required to identify and use the correct information
- Optimised spare parts logistics turns out to be quite difficult
With an interactive spare parts catalogue you achieve:
- All spare parts and service information are bundled in one system
- All data is always available and retrievable
- Identification within seconds
- Automated data comparison with one or many backend systems (for e.g. with ERP/PDM and E-Commerce)
- Production of all catalogue media from one data pool
- Improved quality and up-to-dateness of spare parts and service documentation
- Faster processing of spare parts orders
- Noticeable relief on service and order hotlines
The Touchpoints of Workforce Management and Spare Parts Catalog
The scenario
- A machine XY of customer Z stands still due to a defect
- According to the order, the service technician should repair the machine XY of customer Z
- The service technician has the order opened in the Workforcemanagement mobileX-MIP for Field Service
- He detects, that a specific material/spare part is needed
- He identifies the spare part and wants to order it, so that he can replace the defected one during his operation
- He wants to report this material requirement to mobileX-MIP for Field Service
What is the benefit for you as a manufacturer or service technician?
- Always find the right information – with short search times when searching for catalogues - spare parts, wear parts, accessories and service information
- Simple navigation and visual identification takes the pressure from your service and order hotline: for a better service quality
- Less incorrect orders: Ordering directly from of the catalogue
- Faster processing of spare parts orders – simple, fast, accurate, all around the clock
- Fewer queries to helpdesk or hotline requests, thanks to clear, up-to-date information: Reduce the pressure on service and order hotline
- Shorter downtimes of faulty devices, machines or systems
- Improved and more efficient service thanks to better information
- Optimised workflow all around spare parts Better provision of info