Networking Aftersales and Technical Documentation: Is the connection worth it?
Aftersales and technical documentation are often considered separately. But there is more overlap than many companies think. This blog post shows the added value that interfaces between the two worlds create for mechanical engineering, and the role that digital twins play in this.
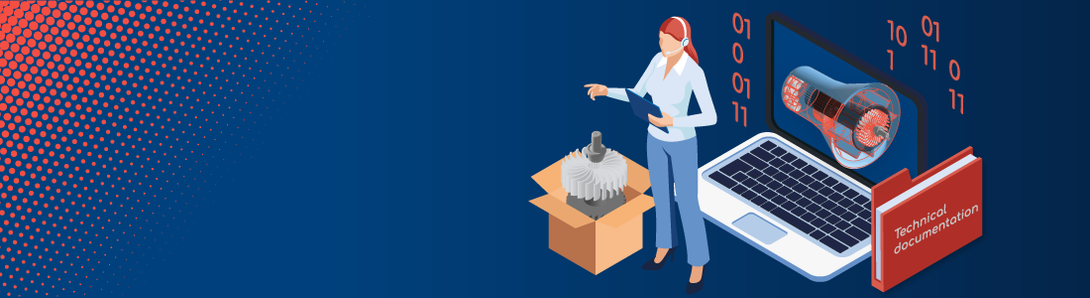
Crisis or no crisis: the times are over when companies spent a lot of money on new machines. For sustainability reasons alone, operators are focusing on using their machines and systems longer and more efficiently.
That is why aftersales and service are becoming increasingly important. Many companies see this as an important driver for their sales growth. Digitalizing service and spare parts management is one of the most important tasks for mechanical and plant engineering. After all, good service is not just an image factor - it is demanded by more and more customers and therefore represents an important purchasing criterion.
Technical documentation also contributes to making the use of a product efficient and safe. To create a solid basis for their economic stability, companies should therefore combine aftersales and technical documentation.
Networking as the basis for further development
As companies' challenges grow, so does the number of processes and systems they need to coordinate:
- In addition to spare parts management and technical documentation, field service management, CMMS maintenance management, ticketing and route planning also play a role.
- Store systems drive spare parts sales.
- Content delivery simplifies the provision of technical documentation.
Each new system and trends such as digitalization and the IIoT lead to a flood of data that companies produce. Their networking and evaluation form the prerequisites for smart services and new business models.
The demand for these is great: customers today no longer buy pure products. They buy services. The goal for mechanical and plant engineering must therefore be "service excellence“. Your service is excellent if it delights your customers so much that they remain loyal to you for a long time and tell other companies about your service.
Excellent service requires excellent processes. This is exactly where the combination of aftersales and technical documentation takes effect.
Breaking down data and process silos
Let's face it: companies are working with an increasing number of increasingly complex processes and data. What is also increasing is the risk of data and process silos. Skilled workers, on the other hand, are in short supply. All of this leads to losses in productivity.
Aftersales and technical documentation must therefore grow together just like other departments in the company. Excellence and performance can only be enhanced if all the cogs mesh. More and more companies are therefore already thinking documentation and spare parts catalogs together.
Nevertheless, both worlds are often still separated from each other in organizational terms. In practice, this is reflected in the different systems that companies use. In the area of maintenance, for example, there are often separate systems for
- Spare parts information
- Maintenance instructions
- Maintenance management
- Ticketing for service calls
If all these systems and their generated data were bundled, it would make service operations much more effective.
How can documentation and spare parts management work together?
Fundamentally, spare parts management and documentation relate to different areas of the product lifecycle. While documentation is often seen as a legal obligation, spare parts management is the free skate that helps leverage new revenue potential.
- The spare parts area looks at the as-built condition of parts and components. Ideally, it includes information on maintenance performed (as maintained). The more up-to-date the information, the easier it is for the service technician to order spare parts. The goal is to have as few discrepancies as possible between the documented and the real condition.
- Technical documentation focuses on general descriptions and often does not refer to a specific part. If machines and systems are offered with various additional packages, the description often refers to only one of the packages. The user must then assess for himself whether a specific component is installed in the machine to be maintained or not. This creates sources of error that cost time and money.
In practice, both a user-friendly product description and the ability to determine the exact part and component are necessary. But only with information from both sources is it possible to achieve an optimal result.
How to successfully network aftersales and documentation
How quickly companies can meet the demand to network both worlds depends on various factors:
- Does silo thinking still exist in the company?
- How high is the quality of the existing database?
- Where does the company stand in terms of networking and digitization?
With the InfoTwin from Quanos, companies can initiate the networking project at any time. The Quanos InfoTwin provides a platform for merging all data required for excellent service. It combines information from spare parts catalogs and technical documentation with current machine and plant data.
The result is a digital twin for aftersales and service that bundles information from technical documentation, spare parts management, and other sources. The following three examples show the added value that Quanos InfoTwin offers.
Linking information
To link spare parts management and technical documentation, interfaces must be identified. To do this, one works with metadata and mapping, for example: The metadata of a chapter on engine cleaning must contain the engine's article number. However, this direct linking only works as long as the article number does not change. If it changes, for example due to a change of supplier, this results in a high data maintenance effort.
InfoTwin offers a more efficient way of linking via indirect links and parameters. In our example, the part number of the motor is not linked to the documentation, but rather the part type "gearmotor" and the output power "180 watts". From the documentation, the parameters can then ideally be used to obtain unique hits or to narrow down the results to two or three options using a filter.
Artificial intelligence
Another approach that can be pursued with InfoTwin in the future is the identification and enrichment of metadata with the help of artificial intelligence. The AI analyzes the content of chapters and suggests metadata. The technical editor checks the result and makes corrections. In this way, the quality of the suggestions improves over time while the effort is reduced.
Intelligent assistant
The combination of spare parts management and technical documentation also offers advantages for on-site service activities. For example, if the InfoTwin accesses step-by-step instructions from the documentation, it can guide the service technician through various processes like an intelligent assistant and support his activities.
The technician receives additional information on suitable wear parts, operating materials or special tools and is offered a direct link to these. Thus, the technician knows how to perform the repair and what he needs for it.
Linking information
To link spare parts management and technical documentation, interfaces must be identified. To do this, one works with metadata and mapping, for example: The metadata of a chapter on engine cleaning must contain the engine's article number. However, this direct linking only works as long as the article number does not change. If it changes, for example due to a change of supplier, this results in a high data maintenance effort.
InfoTwin offers a more efficient way of linking via indirect links and parameters. In our example, the part number of the motor is not linked to the documentation, but rather the part type "gearmotor" and the output power "180 watts". From the documentation, the parameters can then ideally be used to obtain unique hits or to narrow down the results to two or three options using a filter.
Artificial intelligence
Another approach that can be pursued with InfoTwin in the future is the identification and enrichment of metadata with the help of artificial intelligence. The AI analyzes the content of chapters and suggests metadata. The technical editor checks the result and makes corrections. In this way, the quality of the suggestions improves over time while the effort is reduced.
Intelligent assistant
The combination of spare parts management and technical documentation also offers advantages for on-site service activities. For example, if the InfoTwin accesses step-by-step instructions from the documentation, it can guide the service technician through various processes like an intelligent assistant and support his activities.
The technician receives additional information on suitable wear parts, operating materials or special tools and is offered a direct link to these. Thus, the technician knows how to perform the repair and what he needs for it.