Spare Parts Management in Mechanical Engineering: 7 Proven Strategies
Spare parts management is a critical aspect of mechanical engineering that is instrumental in minimizing machine downtime and maximizing productivity. In this blog article, we present seven proven strategies you can use in spare parts management to achieve maximum availability and cost efficiency.
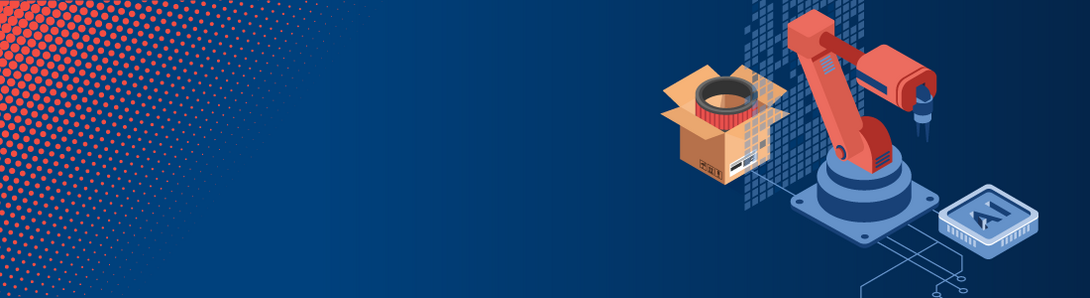
1. Establishing an efficient inventory management
Efficient inventory management is the key to successful spare parts management. By implementing inventory control systems and regular stock checks, you can ensure that you always have sufficient quantities of spare parts to deal with potential machine failures quickly and effectively.
2. Identifying critical spare parts
Identifying critical spare parts that can cause significant production downtime if they fail is critical to an effective spare parts strategy. By analyzing machine data and considering factors such as probability of failure and impact on production, you can build prioritized spare parts inventories to avoid machine failures and extended downtime.
3. Using predictive analytics
Predictive analytics can help you predict spare parts needs and take proactive action. By using sensor data and machine learning, you can identify potential failures and selectively deploy spare parts to prevent or minimize machine downtime.
4. Developing a spare parts procurement strategy
A sound spare parts procurement strategy is critical to ensure you can obtain the spare parts you need in a timely and cost-effective manner for your maintenance operations. This includes identifying reliable suppliers, establishing ordering processes, and implementing supply contracts to ensure optimal pricing and delivery times.
5. Optimizing warehousing and logistics
Optimizing warehousing and logistics helps to manage spare parts more efficiently and reduce costs. This includes the implementation of efficient warehousing systems, the use of advanced logistics solutions, and cloud-based software applications to monitor and control spare parts inventory and the supply chain.
6. Employee training and continuing education
The competence of your employees is critical to effective spare parts management. Invest in training and education to ensure that your employees have the knowledge and skills needed to effectively identify, procure and manage spare parts. This not only helps improve the efficiency of your spare parts management, but also increases employee satisfaction and motivation.
7. Implementing digital tools and technologies
Using digital tools and technologies can significantly increase the efficiency of your spare parts management. By using software solutions, IoT devices and mobile applications, you can collect and process real-time data about the condition of your machines and spare parts inventory. This enables faster identification of spare parts needs and more effective planning and control of your spare parts procurement and inventory management processes.
Demand for spare parts identified. And now?
What's the best way to find the spare part you need?
The easiest way for a service technician, maintainer or customer to identify the spare part they need is to use a digital spare parts catalog. One of the key functions of a digital spare parts catalog is to enable a quick and intuitive search for the required spare part. A digital spare parts catalog offers visual, structural and textual search options for this purpose.
How does this look in practice? Visualizations of the spare parts in 2D or 3D format, QR codes on the machine, and extensive text search options support the search for the desired spare part in the digital spare parts catalog. In addition, only parts that are installed in the selected machine are displayed in the catalog. The information is clear and unmistakable.
The result: 20% fewer incorrect orders.
Learn more about this in our eBook.