Benefits of using 3D Data in the Manufacturing Industry: 3 examples
When 3D models are used in digital spare parts catalogs, they bring assets and their assemblies to life. This article summarizes who benefits in manufacturing companies and beyond, and how 3D data can be used outside of design and construction.
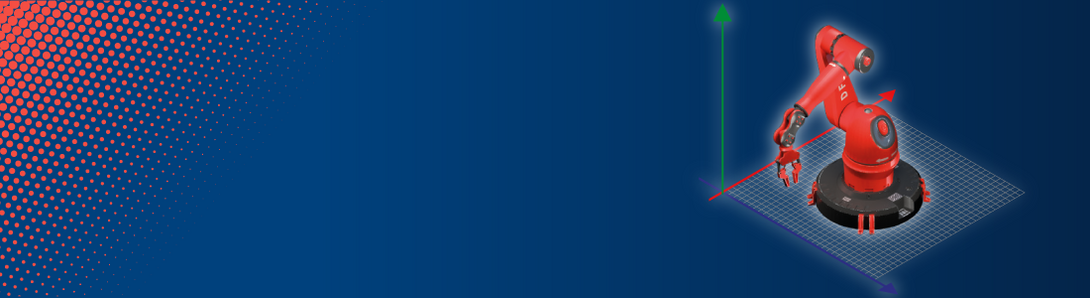
Catalog systems that enable machine and plant manufacturers to create and publish digital spare parts catalogs offer various options for handling 3D data. This benefits various user groups within the company as well as manufacturers' customers. The following usage scenarios show the range of possibilities offered by integrating CAD visualizations in spare parts catalogs.
Easy Data Preparation
Design data and technical documentation link product development to product application. Both play an essential role in the realization of products and their maintenance. The user-oriented preparation of design data is therefore relevant for every after-sales business.
The easier and more efficient data preparation works, the more time and costs companies can save. A 3D spare parts catalog allows employees outside the design department to prepare data independently and use it for their own work.
Use Case Technical Writing
The task of technical writers is to prepare complex technical information in a way that is comprehensible to the users of a device, machine or system. With the help of 3D data, they are able to create graphics from different angles or animations for repair and assembly instructions without the support of product design or engineering.
Better Understanding of Complexity
3D models are always indispensable when it comes to presenting complex products in a comprehensible way. In the industrial sector, they are the key to mapping even large plants in such a way that even employees without engineering degrees can find their way around them. They can more quickly grasp how individual machines and components are connected and where they are located.
Use Case Sales Department
The clear and simple visualization of components of a machine or system simplifies the work of customer advisors. With three-dimensional models, they have the opportunity to present various machines, devices and systems to their customers in such a way that their advantages and special features can not only be grasped more quickly, but can be experienced directly.
With advancing digitization, companies can even go one step further and expand 3D visualizations into augmented reality and virtual reality.