State of the Art - Digital maintenance management and predictive maintenance
We are a software company that supports operators of machines, equipment and plants to digitize and optimize their maintenance and service processes.
Being an operating company, you have to take care of the ongoing operation of your machines and plants - and reduce downtimes to a minimum. The autonomous identification of spare parts and the corresponding documentation is essential for this.
Expensive and time-consuming maintenance
You are an operator of machines, plants or vehicle fleets and need to keep your capital goods in good operating condition. Your primary objective is to avoid operational disruptions and thus unnecessary downtimes of machines and plants. However, repair and maintenance require considerable resources. You are under constant pressure to reduce costs and make processes more efficient.
Digital spare parts and service information system: Quanos SIS.one
Our standard solution Quanos SIS.one helps you to master these challenges. We offer you an all-in-one system that gives you a 360° view of your fleet, machines or plants. All information from the various manufacturers as well as on machines and plants flows into the digital system and is centrally available in a service portal.
The service information system links all data across all systems and thus enables efficient use when preparing, planning and performing maintenance.
1. Precise, accurate search for spare parts and information
Maintenance staff who depend on precise documentation and simple parts searches can thus access centrally maintained operating and maintenance instructions, schematics, work values, stock levels and information on spare and wearing parts at various locations at any time. They identify the required part immediately and can order it directly from the system.
The browser-based solution can even be conveniently operated from mobile devices. The easy, 24/7 access to current, exact technical data saves time and money.
2. Documented knowledge and experience
In addition, process documents, training videos, updates and security warnings can refer to product models, documents or even individual components - so service and maintenance personnel can find the required content at the right time.
The documentation of performed maintenance work, empirical values and in-depth detailed knowledge of individual employees can be stored as notes and made available to the team in a central location. This increases employee productivity, improves internal knowledge and extends the service life of the machines.
No more time-consuming searching and ordering
Our customers tell us that their maintenance technicians had to spend 20-40% of their working time searching for and ordering spare parts or spare parts information before using a service information system. They had to search through different systems or contact the respective customer service department. That is over now.
3. Cost savings through easy identification of alternative spare parts
After the warranty period has expired, the purchase of alternative spare parts can lead to considerable cost savings compared to expensive original parts. Alternative spare parts may also be available more quickly. The interactive catalog system uses linked data to show the user which alternative parts are available - including price and delivery time.
Once the system is fully integrated, the employee can order the selected part directly from the system - and downtime is reduced to a minimum.
4. Lay the foundation for predictive maintenance
Your goal is to predict future maintenance requirements by permanently monitoring machines and systems and thus plan maintenance processes in the best possible and most efficient way? With the digital spare parts and service information system, you will establish the basis for this. You create an intelligent data model of your machines and systems - a so-called "Digital Information Twin" -, link IoT data with spare parts and stock levels and optimize your processes.
Via the central portal for all maintenance information and processes, you create a comprehensive, digital understanding of your machines and systems.
Our customers about us
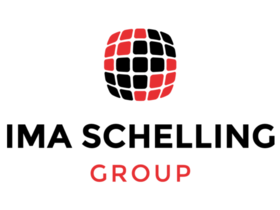
„With the integration of electrical and pneumatic circuit diagrams in our spare parts catalogues, we provide an 'all-round information and ordering system' that supports our customers in all areas of spare parts research and ordering in a professional manner.“
IMA Dirk Münze | Technical Documentation
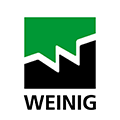
„We are very pleased that SCHEMA ST4 is running on the web. Switching to ST4 in the cloud was the ideal step for us not only to advance the WEINIG Group's digitization strategy in technical writing as well, but also to bundle resources and optimize group-wide communication. The editorial processes could be harmonized across all locations.“
Weinig Grecon GmbH & Co Dr. Rainer Vollmer | Chief Information Officer
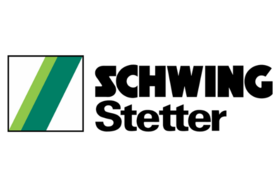
„[...] We are convinced that, with CATALOGcreator®, we have found and introduced a modern and innovative software solution for our spare parts management.“
SCHWING Stetter Werner Herling | Manager of Technical Documentation and the Service / Technical Office