Sparked interest?
Steinecker GmbH
Intuitive Spare Parts Catalogs for Customized Brewery Systems
Many master brewers rely on technology from Steinecker to ensure that their beer delivers the same distinctive taste every time. The Bavarian-based plant manufacturer helps breweries to plan and maintain their complex systems. And these customers can now access digital spare parts catalogs in the Steinecker.Shop to give them a better overview of spare parts and the documentation.
Steinecker: technology pioneer helps to ensure great-tasting beer
Steinecker GmbH is where tradition meets high-tech. Through its sophisticated brewing technology, the plant manufacturer based in the German town of Freising helps to ensure that Bavarians and beer-drinkers from around the world get to enjoy first-class beer.
Ever since the company was founded by the engineer Anton Stecker in 1875, it has combined progress and quality in the brewing process. Today, Steinecker is part of the Krones Group and, with a team of experts numbering over 400, it focuses on building the best possible systems for customers in more than 160 countries.
Steinecker’s Lifecycle Service looks after plants from the very beginning of their lifespan to the very end. It ensures that the systems keep running for a long time and that customers receive the right spare parts for maintenance as and when they need them.
Challenges: a clear objective and complex information
The breweries that Steinecker supplies with equipment all have the same goal: to supply their customers with delicious beer. However, the processes in the background are anything but standardized – even in Germany where the Beer Purity Law is in force. “To date, no two of our systems are the same,” reports Johanna Parzinger, aftersales project coordinator at Steinecker GmbH.
The different recipes and ingredients, and the varying methods involved mean that customers use a variety of different tanks and fittings. Brewery systems also often have to be tailored to the specifics of the brewery building itself, which is why each system has to be unique.
Steinecker’s technology can also be used in other food sectors, such as producers of cultured meat and dairy alternatives, or in the wine and spirits sector. Different safety requirements and regulations apply in these sectors from those that apply to breweries.
The uniqueness of the Steinecker systems delivers the best results during brewing, but it also results in a high degree of complexity in spare parts management and in the technical documentation. A simplified representation of brewery systems is not sufficient when it comes to searching for spare parts or documents.
The flow of information: from the flow chart to the digital spare parts catalog
“That is why we use piping and instrumentation flow charts that are linked together,” says Parzinger. The flow charts show which valves and pumps are installed in a system. Each individual component has a unique function number that can be used to reliably identify spare parts.
These flow charts are a permanent fixture, supporting customers and the Steinecker teams from the initial inquiry to the end of the machine’s life. Whether in the engineering department, when looking for spare parts, or when reworking parts, the flow chart is a central element.
And, however complex the customers’ systems are, the associated documentation is equally complex. Steinecker supplies system-specific documents on USB sticks or, at the customer’s request, in hard copy format. The USB sticks provide the equipment and material documents in a folder structure.
In mid-2023, Johanna Parzinger and her team opted to switch to digital spare parts catalogs to enable both their colleagues in the Service team and customers to access spare parts information and the technical documentation more quickly when they need it. The flow charts were to be used as the basis for this.
What were Steinecker’s objectives for the digital spare parts catalogs?
The objective was to reduce the level of complexity in Aftersales and Technical Documentation and to enable customers to achieve better maintenance processes through a modern online shop.
The spare parts catalog systems needed to meet the following requirements:
- Strong customer focus: Steinecker has nearly 200,000 parts in store at the Krone Group’s German sites and in spare parts centers around the world. To ensure that customers only see the spare parts that are relevant for them, an interactive display of the customer-specific system was an important element of the brief.
- Digital shop features: Another key priority was that users of the spare parts catalogs should not just save time searching through them but also during the check-out process, so that project coordinator Johanna Parzinger and her team would have to spend less time dealing with support requests.
- Transparent documentation: The objective was for the operating manuals and TÜV certifications to be permanently accessible for customers online, both for the entire installation and for individual sections.
Up and running with Quanos in the space of a year
The Steinecker team is using the Quanos SIS.one software solution as the technological basis for the spare parts catalogs. The time from Steinecker’s decision to work with Quanos to when the Steinecker.Shop went live was less than a year. During this period, Steinecker successfully overcame many challenges together with Quanos:
- Steinecker’s IT team did not take much persuading of the benefits of the project, as the company’s IT infrastructure was already being hosted by Quanos. This meant that Steinecker avoided having to purchase and operate its own server solutions.
- During the concept phase, the aftersales project coordinator and her team confirmed what was possible with the existing data and the Quanos spare parts catalogs. First, the data was to be imported into the system without interfaces – even in this configuration, various forms of automation were possible, and the Steinecker team were able to implement the desired functions without any problems.
- One particular challenge was ensuring that hotspots for the flow charts were transferred across to the catalog system. The hotspots are linked to the function number for the relevant parts. In-house development is a key USP for Steinecker. With support from Quanos, the hotspots were successfully transferred to the catalogs.
Improvements from working with Quanos
Once the key functions had been implemented, Steinecker was interested to find out the customers’ perspectives: “We uploaded simple customer projects and obtained feedback on them,” explains Johanna Parzinger. “This helped us to ensure that we are not losing sight of the customer during the development process, but are meeting their needs.”
And she and her team were successful here too. Their customers are satisfied and are easily able to find their way around the new platform. This is partly due to the fact that Steinecker is using the same structures as they previously used for the USB sticks in the spare parts catalogs, making it a seamless transition for customers.
From the flow charts they are already familiar with or the parts list, customers can directly access documentation, view operating manuals, or place spare parts directly in their shopping carts, and complete their orders efficiently with a standardized checkout process.
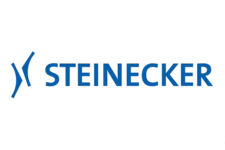
Steinecker GmbH
„We uploaded simple customer projects and obtained feedback on them. This helped us to ensure that we are not losing sight of the customer during the development process, but are meeting their needs.“
Mechanical and plant engineering