Data Quality: When It Comes to Digital Spare Parts Catalogs, How Good Is Good Enough?
Are you keen to get started with digital spare parts catalogs and service portals, but you’re concerned that the quality of your data is inadequate? We'll show you why your database doesn't have to be perfect to move your service processes into the digital fast lane.
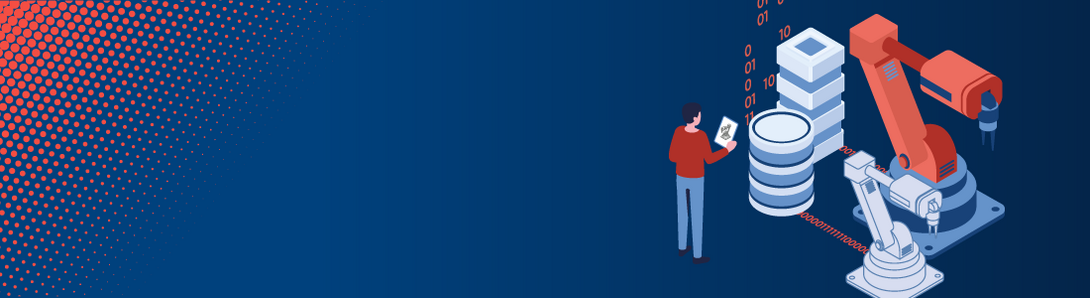
Why data quality is key when creating spare parts catalogs
Digitalization is progressing at speed. For machine manufacturers and plant operators this means that there’s no way of avoiding tools such as the digital spare parts catalog. Packed full of service information, it serves as a central starting point for technicians, customers, and service employees, and forms an important basis for the digitalization of your service processes.
Spare parts information that is available 24/7 and linked to the technical documentation, coupled with the ability to order parts online, speeds up many processes that used to take days.
However, if spare parts catalogs are going to save you lots of time when marketing spare parts and during service calls, they must be founded on an accurate, up-to-date, and consistent database. Furthermore, there must be no inconsistencies between the mobile and web view and different sections of the catalog.
The upshot of poor data quality
Machine manufacturers must take a number of precautions to make sure that their catalogs offer added value for users, and to support them in finding solutions for their problems. These precautions include correctly creating and maintaining the data.
A failure to do so brings with it a number of risks:
- Incorrect orders if article numbers or technical specifications are wrong
- Confused and irritated customers if prices or delivery times are displayed incorrectly
- Inefficiency of your processes because customer service personnel and technicians are continuously required to correct orders or update data manually
Deficient data quality costs both your customers and your team time and means that they miss out on valuable potential sales.
Particular data challenges in machine construction
To improve data quality, the data required for spare parts catalogs should be correct from the time that it is entered and must then be consistently usable. You should therefore keep the manual input of data to a minimum and avoid data silos.
However, this is easier said than done, in particular when it comes to machine construction; information about spare parts and components often comes from different sources in the company, for which data had to be prepared in different ways. Typical sources include the ERP system, technical documentation, and the PLM system for example.
The challenge is to free all this information from its silos and transfer it to the digital spare parts catalog in a consistent and user-friendly format. The easiest way to take care of this process is with a central platform for service data.
Are you looking for a system that synchronizes and improves your service data? Then familiarize yourself with Quanos InfoTwin.
How to guarantee adequate data quality in your spare parts catalogs
Are you concerned that your data are not yet ready to serve as the basis for digital spare parts catalogs? Then allow us to reassure you that “nothing is perfect”—this is especially true of machine manufacturers’ data.
In many organizations, IT systems and databases have grown over many years and more than half of companies are still a long way from finally eliminating their internal data silos. However, instead of wasting months breaking down these silos and cleaning out existing spare parts and service data, you can drive service transformation and data cleanliness in parallel.
Don’t focus solely on your database. Instead, use your digital spare parts catalog project to drive data quality and digitalization forward in parallel. This will allow you to continuously improve your data and gradually free it from its data silos. Our practical guide on the subject of data quality shows you the easiest way to proceed with this.
Long-term benefits of a digital spare parts catalog
If you succeed in improving your data and incorporating it into the digital spare parts catalog, your customers will be able to identify the spare parts they need more quickly and order them directly. Incorrect orders, returns, and the costs per order decrease, while sales and turnover increase.
For machine manufacturers, the digitalization of their spare parts catalogs with a solid database also opens up new business opportunities—they can use the catalogs as a foundation for service portals, in which all aftersales information flows together in the future. With this, data silos become a thing of the past and are replaced by a single source of truth.
The next step - further improve data quality
You don't need to have perfect data right from the start to finally put your digitalization plans into practice. In most cases, your existing database is sufficient.
Would you like to find out more about how to digitalize your spare parts catalogs with existing data and ensure high data quality at the same time? Our free practical guide for enhanced data quality offers you specific recommendations on how to proceed and introduces you to useful tools with which to successfully launch your digital service transformation.