The Costs of Machine Downtimes and how to reduce them
When machines break down unexpectedly, companies suffer massive financial losses. However, many manufacturers are unaware of the real price they pay for downtimes. In this blog, we will illustrate how high the costs of machine downtimes are and how you can avoid expensive stoppages in production.
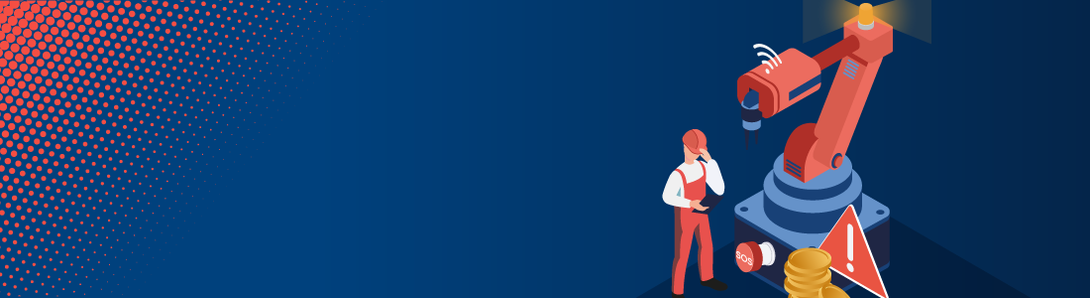
What are machine downtimes?
Maschine operators experience planned and unplanned downtimes. Both generate high costs. However, regular downtimes during which machines and systems are serviced can be scheduled in a budget-friendly manner. This is not the case with unexpected downtimes: During these periods, machines and systems break down without warning, resulting in a loss of production and revenue. Unplanned downtimes can be caused by various factors:
- insufficient transparency about machine conditions and thus unrecognized wear on parts
- inefficiently planned service assignments
- inadequate maintenance due to knowledge gaps or a lack of tools
- human error due to a lack of training for employees
- defective, missing or incorrect spare parts
Manufacturing companies should therefore actively get to the bottom of the causes of their machine downtimes. After all, downtimes not only threaten turnover: Companies have to invest time and money in machine restoration and are therefore less productive.
How do you calculate the costs of machine downtimes?
Planned and unplanned downtimes can cost companies up to ten percent of their available production time. This time, as well as the money that manufacturers have to invest in troubleshooting is irretrievably lost.
But do you know what one hour of downtime costs your machines? If not, you're now on the right track: according to the International Society of Automation (ISA), 80 percent of companies are facing the same issue.
What production managers often fail to consider is that, in addition to the direct costs, i.e. the loss of sales, downtime costs also include a number of hidden costs. The following indirect costs are the reason why machine downtimes are so financially painful:
- Unplanned costs are incurred for maintenance work by external service technicians and for resources to rectify faults.
- Production capacity is not fully utilized, but fixed costs are still incurred during the downtime, for example for wages or operating resources — this reduces the profit margin.
- During a breakdown, sales opportunities are lost or customers have to wait longer for their goods.
- In the food industry, a machine breakdown can mean the loss of material if perishable goods are being processed.
- Repairing and restarting machines causes expensive overtime.
- During downtime, employees have to put their energy into solving the problem, which reduces productivity. The ISA estimates a five to 20 percent loss in productivity.
- Downtimes in production also affect machine and plant manufacturers: The downtimes of their machines can have a negative impact on their reputation.
How expensive are machine breakdowns?
The predictive maintenance specialist Senseye, which now belongs to Siemens, has calculated the concrete costs of machine downtimes:
- The hourly costs for system failures quickly exceed the 100,000 dollar mark — the equivalent of more than 90,000 euros.
- On average, there are 20 breakdowns per month per plant, resulting in 25 hours of lost production time.
- Large plants have to dig particularly deep into their pockets when breakdowns occur: With an average of 323 lost production hours, they lose around 157 million euros per year and plant.
- Broken down to the hour, large companies pay around 490,000 euros for lost sales, machine restarts, and repairs.
- Overall, the Fortune Global 500 industrial companies lose eleven percent of their annual turnover due to unplanned machine downtimes — just under 1,380 billion euros. By way of comparison, in the 2021 report the figure was around 797 billion euros.
This is how much unplanned downtimes cost in various industries
The costs of machine downtimes are increasing — especially in times when companies are facing crises and difficult financial markets that are making them cut costs. It is therefore not just the big players that should do their best to keep their machines running: Higher plant availability is beneficial for all industries.
These are the costs incurred by defective machines and systems in various industries:
- The cost range for one hour of downtime in the industries surveyed ranges from the equivalent of almost 36,000 euros in Fast Moving Consumer Goods to 1.84 million euros in the automotive sector.
- In the oil and gas sector, downtime costs doubled by 50 percent between 2019 and 2022 to around 460,000 euros.
- The total annual costs for unplanned downtimes in large automotive plants average more than 550 million euros each.
- In heavy industry, metal processing and mining, the figure is 118 million euros per plant, while in the oil and gas sector it is around 137 million euros.
Incidentally, downtimes are also costly in IT-based industries. Figures from 2016 show that downtimes in data centers cost an average of 8,300 euros per minute.
Escaping the cost trap: How to avoid machine downtimes?
When you are fighting to avoid downtimes, knowledge is your most powerful weapon. The first step is to become aware of the consequences and costs of machine downtimes and to understand that downtimes are expensive and that investment in essential maintenance is required.
Next, the causes of downtimes must be identified and avoided by means of routine maintenance. According to Senseye, for example, 72 percent of industrial companies want to reduce their downtimes by means of predictive maintenance.
Instead of repairing when necessary, preventive maintenance means that maintenance work takes place regularly and is planned in advance. To achieve this, it is important to provide service technicians with all of the relevant machine and spare parts information so that they can efficiently troubleshoot downtimes.
Reducing machine downtimes: This is how software helps
By means of the analysis of system failures and optimization potential or the elimination of machine defects, software solutions provide manufacturers and machine operators with the necessary transparency about machines and processes.
The digital twin plays an important role here. It maps the machine and system status over the entire life cycle and combines it with information on completed and planned maintenance processes, technical documentation, and information about spare parts.
Digital twins such as the Digital Information Twin (DIT) from Quanos are a prerequisite for efficient service operations. As a central knowledge platform, it not only provides important information for maintenance tasks but also offers intuitive step-by-step instructions on how to troubleshoot defects more quickly.
Because all the necessary information is connected, digitized, and available in real time, technicians can access it via mobile devices such as smartphones or tablets and efficiently complete repairs. Service staff are relieved of these tasks and can get back to other tasks more quickly.
Discover the most effective tool against machine downtimes Quanos InfoTwin!
Increase turnover, reduce downtimes and maintenance costs
Companies that are familiar with the costs of downtimes know that investing in solutions is worthwhile if they can avoid even a few expensive minutes of downtime. According to BearingPoint, strategies such as predictive maintenance allow companies to increase turnover by 10 percent and save 17 percent on maintenance and service costs.
It is true that unplanned downtimes cannot be completely avoided. But with the right software solution, you can significantly increase the availability of your systems. This will protect your company from production downtimes and save you the direct and indirect costs of machine breakdowns.
With the all-in-one solution InfoTwin from Quanos, you give your service technicians the tools they need to rectify faults more quickly. This includes easy-to-understand instructions, clear documentation, and the ability to quickly identify and order spare parts.