Three Reasons Why You Should Start Using IIoT Service Portals
Industrial companies invest billions in their digital transformation, but the outcome often doesn’t live up to their expectations. Those who would rather take a gradual and sustainable approach to digitalization would be better served by service portals based on IIoT technologies.
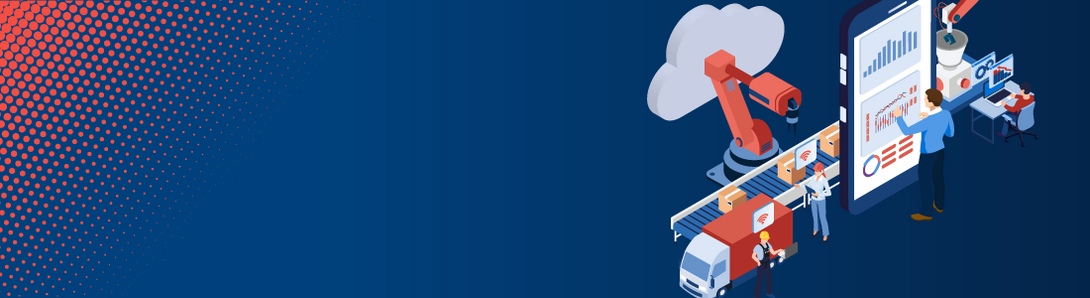
The digital transformation in industry: large investments, little progress
The digital transformation is in full swing in the mechanical and plant engineering sector. In their bid to keep pace with Industry 4.0, industrial enterprises around the world are investing over one billion euros a year in digital transformation solutions. Commercial applications range from quality and maintenance analyses through automated KPI monitoring to digital twins.
Yet despite all this, the transformation itself often lags behind expectations. Sixty-three percent of companies investing in digitalizing their processes say they are having difficulties integrating new technologies. Over half of the industrial companies cannot exploit the potential of their data as they lack the personnel or their database is not structured enough.
Machine manufacturers need solutions that can be seamlessly integrated into their data landscape and offer easy access to digitalization in order to effectively overcome these challenges. IIoT-supported service portals—a platform for machine and service data, which integrates industrial assets with the functions of the Industrial Internet of Things—are one such solution, and there are a variety of reasons why they can help, three of which we highlight here.
White paper: IIoT Portals for Your Digitalization
You can find out everything you need to know about service portals with IIoT functions and the advantages these platforms bring for your spare parts information and aftersales service in our free white paper on IIoT-supported service portals. Download it now to open the door to digitalization!
Reason No. 1: IIoT service portals increase your service efficiency thanks to real-time data
One of the biggest benefits of IIoT-supported service portals is being able to integrate real-time data from machines and equipment, as manufacturers and operators can continuously monitor the status of machines.
Maintenance processes are one area that can be improved as a result, whereby real-time data allows problems to be detected early so that technicians can act proactively. If a machine is showing signs of wear, the technician can order the spare parts they need and carry out repairs in a way that minimizes disruption to the machine’s operation.
A good portal solution ensures that the information needed for this is seamlessly interconnected and is even able to work with unstructured data.
Reason No. 2: Portals open the door to new business models
IIoT service portals not only offer technical advantages, but also economic ones. Integrating data from IoT devices into service portals enables machine manufacturers to develop new services.
Thanks to IIoT technology, manufacturers can offer data-based services as pay-per-use or subscription models and generate additional revenue, for example, with proactive and predictive maintenance.
Reason No. 3: IIoT platforms improve customer loyalty
Today, customers in the plant and machinery construction industry not only expect high-quality products, but also excellent service. IIoT-supported service portals improve service quality significantly by helping technicians and customers solve problems efficiently.
By integrating IIoT data into service portals, service staff can respond more quickly to customer enquiries, and technicians can plan and perform their service visits more effectively. This in turn reduces the number of service visits required, increasing customer satisfaction.
Now is the perfect time to start using IIoT-supported service portals
The digital transformation poses a challenge for many manufacturers and operating companies, especially when it involves integrating new technology. Recent surveys show that no industrial companies in Germany have managed to fully implement Industry 4.0, and that many organizations are still using basic technology.
Do you want to achieve your digitalization goals quicker than others, improve your service, and increase your revenues to boot? Service portals with IIoT functions are a good starting point for your digital transformation, as they enable you to connect data sources from your service operations and machines to use as a basis for digitalization.
When embarking on this step, it’s important you employ the right technology and experienced software partners. If you would like to find out more about the advantages IIoT portals bring to the machine and plant manufacturing sector and how Quanos and elunic can help you implement them, check out our free white paper.