Is working with a Component Content Management System really easier?
Do I implement a Content Management System, yes or no? We are often asked this somewhat philosophical question, so we now want to provide a more specific answer. Imagine two technical writers working together in a team in a medium-sized organisation.
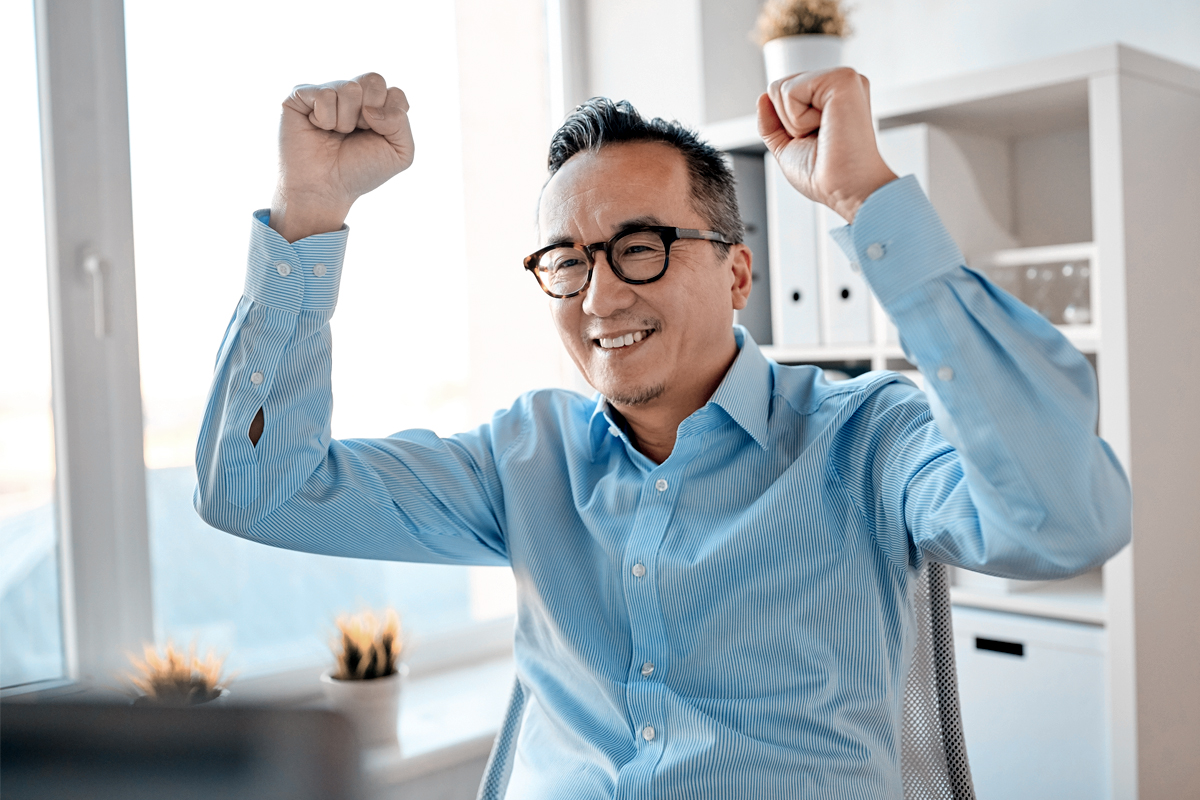
We’ll call them Thomas and Katherine. Both of them are responsible for the documentation for a range of washing machines. The difference between them is that Thomas continues to draft his operating instructions “by hand” in Word, whereas Katherine uses a Component Content Management System (CCMS).
Let’s shadow each of them in turn in their day-to-day work. Where exactly are the differences in their respective working methods with and without a CCMS? Are the differences really that great?
New input for the manuals
Thomas and Katherine are briefed at a meeting with their product managers:
- a range of washing machines has been enhanced with a function for removing pet hair.
The operating instructions need to be updated accordingly, which affects some text and graphics. - The operating instructions then need to be approved and translated into English.
- There are two print formats for output: one variant, in A5 format, for the full, maximum content and one variant, in A4 format, to reduce the content to a double-sided quick guide. And both formats are also required for each language.
Let’s begin by taking a look at Thomas’s approach using Word.
Day-to-day technical writing without a Content Management System – a labour of love?
Drafting texts
Thomas sits at his computer and opens the folder where he has stored the previous version of the operating instructions as a Word file and the relevant graphics that need to be amended. Before he begins writing, he saves a backup copy. He then searches through the whole document from start to finish for the sections to be updated and also begins to add the new content.
Quality assurance, approval and translation of the operating instructions
Once he has finished his draft, Thomas forwards the content for quality assurance and technical approval. Katherine is available and checks Thomas’s document for authoring accuracy, to ensure consistent use of formats and wording. The product manager then checks the content for technical accuracy and writes any changes required into the Word file.
Thomas can then approve his operating instructions: To do this, he asks the technical person responsible to sign a form and saves the latest version of the file on the drive. He then sends the file to the external translation agency for translation into English. From the translated content, he now has to manually compile the quick guide for the A4 variant – a job involving more work for QA.
Publishing the operating instructions
All that Thomas needs now is the layout for the different output formats. He has drafted all the content for the A5 variant in German and English, each in a separate Word file, without any changes to layout. So he now needs to compile layouts for the German and English A5 variants. With the quick guides in A4 format, which are also both in German and English, that makes another 2 files. So, 4 layouts that he needs to compile manually according to the organisation’s layout. That really does take a lot of time. Finally, Thomas passes the operating instructions to his product manager for a final check and thus for official approval.
Day-to-day technical writing with a Content Management System – more management than writing?
Drafting texts
After the meeting with her product manager about the new function on the washing machines, Katherine goes to her workstation and opens the CCMS on her computer, into which she migrated her documentation some time ago. Since then, she has exclusively been compiling content using the system. As her data has been stored on a server since she switched to the new system, and because she has assigned version numbers to everything belonging to a particular status, previous versions can be retrieved at any time – she doesn’t need to make any backup copies.
In a CCMS, documents are only created at the time of production. Individual “sense units” in the document have previously been stored in the system as modules, nodes or components. This means that the same text components can be assembled as required for different application scenarios.
So, to update content, Katherine just needs to open the relevant text or graphics component and add the information about the new function. She only needs to do that once, as she will be able to reuse the components, so there is no need for any tedious copying and pasting. At the same time, she assigns some metadata to her new content, for example, the types of washing machine for which the content is applicable, so that she can subsequently filter out any content that does not apply to a particular type of washing machine.
Quality assurance, approval and translation of the operating instructions
After she has updated the new content, Katherine initiates an automatic check of sentence structures and section formats in the Content Management System. The check follows Schematron rules that she herself has specified. Meanwhile, she also checks Thomas’s operating instructions. For the technical check, she sends her product manager a link to the updated and new content in the Content Management System. The product manager reads this – and only this, because everything else has already been approved in a previous version – and comments directly in the components. After any amendments, Katherine can approve the operating instructions in their current status.
The next stage is the translation into English. To do this, Katherine runs a TMS export from the Content Management System and sends it to the translation agency. This only contains content that is not yet translated, which saves time and money. Katherine can run a TMS import of the finished translation into the Content Management System. By doing this, translated content is automatically linked back to the content in the source language.
Publishing the operating instructions
Katherine now uses the text and graphics components to create a structure for the full A5 variant and then uses the same components to create a structure for the pared-down A4 variant, which contains only the key content. This tells the system which content needs to be used where, in which variant. Katherine has precisely specified the layout for the two variants. They are automatically applied at the time of production to the content and structures, so Katherine does not need to think about them again.
For the English documents, Katherine just needs to switch the language and then click on that to produce further copies.
To use or not to use a Content Management System – that is the question
Even though the aim of their job and information acquisition remains the same, the ways in which the two technical writers work share few similarities. Right from the moment when Thomas and Katherine begin compiling their new content, their approach to the work was completely different. Working without a Content Management System certainly gives technical writers more freedom, but like all manual processes, it takes a lot of time – especially when it comes to working in a team.
In the CCMS, the world looks completely different: Katherine only has to create the layout once; after that, she can reuse it for each subsequent production. The system also supports her with quality assurance and translation management.
If you would like to find out more about the advantages of a Component Content Management System, visit our website for further information or sign up for a free webinar.
Other articles from Quanos
This might also interest you
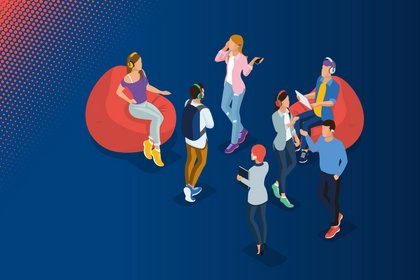
„Doku-Lounge“: Auf dem roten Sofa mit Kerstin Berke und Philipp Eng
Moderatorin Kerstin Berke und Marketingspezialist Philipp Eng sind das Duo vor und hinter dem Mikro der „Doku-Lounge“…