Cloud Platform for Mechanical Engineering: A Single Location for Aftersales and Service
To optimize internal processes, more and more machine and plant manufacturers are switching to software solutions in the cloud. The advantages of a cloud platform can also be leveraged in the area of service. This article summarizes and explains these advantages.
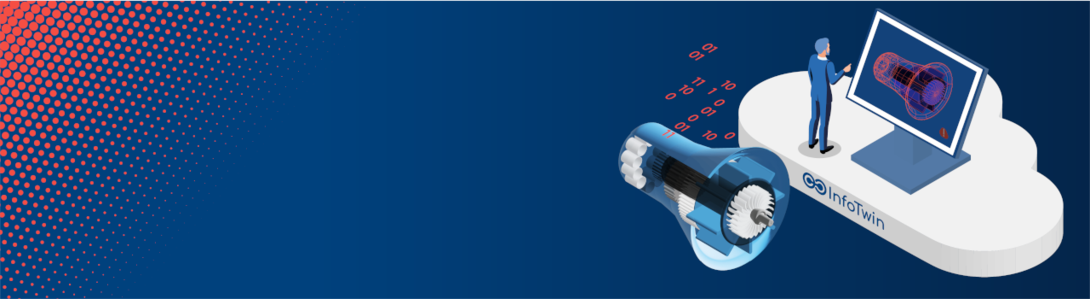
The focus in mechanical and plant engineering is shifting from the manufacture and sale of products to downstream services. The decisive factors in this development include the following facts:
- Industrial customers are placing increasingly high demands on the support and service provided by machine and plant manufacturers. As a result, the number of customer interactions with manufacturers is steadily increasing.
- In times of economic uncertainty and declining sales of new machinery and equipment, the areas of aftersales and service offer potential for implementing new business models. That can not only stabilize sales but also help to develop new target groups.
First-class customer service and new business models can only be implemented through the digitalization of aftersales services. Current trends in aftersales services show what is already possible. However, they also reveal what challenges still lie ahead for machine and plant manufacturers, for example in the form of big data and augmented reality.
The future is in the cloud
Companies that rely on cloud services today are much more relaxed about the future and new trends. With the help of the cloud, even small and medium-sized enterprises (SMEs) are able to digitalize their aftersales services despite cost pressure and demographic change and offer their customers smart services such as predictive maintenance.
To ensure that manufacturers and plant operators benefit equally, machines and plants must be networked. In addition, the active sharing of information between machine manufacturers and plant operators is a strong requirement. After all, data from the field and information and empirical values from the machine builder are all needed to predict the maintenance requirements of a machine as accurately as possible.
This networking is made possible by a cloud platform. It ensures that the necessary data is up to date, networked, and available to every technician who needs to work with it, on both the manufacturer's side and the operator's side.
What is the difference between the cloud platform and an on-premise solution?
In the past, many companies primarily used on-premise solutions for their software. Those who opt for this model buy or rent software that is run on servers in a company-owned or third-party data center. The users are responsible for the hardware and its maintenance as well as for the software updates.
Today, however, cloud solutions are increasingly competing with the on-premise model. Software is provided as a service and thus routinely referred to as Software as a Service (SaaS). Providers of cloud software host it on their own servers. Users access it via their web browser and usually pay a monthly fee.
Both variants have advantages and disadvantages, and deciding which solution is ultimately the right one depends on the individual requirements of each company. As a result, a combination of cloud and on-premise solutions has become established in many organizations.
The status quo: The long road to the service cloud
In order to adapt to constantly changing business processes, increasing customer requirements, and new technology trends, companies must make sure that their software tools are flexible and agile. More and more large and small organizations are therefore moving part of their business processes to the cloud.
In the long term, a mechanical engineering cloud has the potential to connect employees, business partners, and customers and to bundle information from different business areas — ranging from product development to sales — in real time and on all end devices. In 2021, according to the German trend study “Nachhaltig geht nur digital” (“Sustainability only works digitally”), 89 percent of companies with 100 or more employees were already using the advantages of cloud computing for internal processes — that’s five percentage points more than in the previous year.
However, only a few companies are exploiting the potential of a cloud platform for digitalizing their service business. According to an Accenture study, almost all industrial companies see the need to digitalize the sale of their machines, spare parts, and services. But the majority of companies, or 80 percent, are still far too slow in implementing the corresponding plans, even though a service cloud offers major advantages for mechanical engineers.
What are the advantages of cloud computing in the area of service?
One unbeatable argument for the cloud is its flexibility. Companies do not have to move to the cloud overnight, but instead can initially use a hybrid solution of cloud and on-premise solutions. They can migrate individual areas of their aftersales operations to the cloud by starting with a Digital Information Twin, for example. Gradually, other areas can be networked and existing tools such as ERP software can be connected.
Service employees can thus be gradually introduced to their new "working environment." Machine and plant data can be networked more easily and centrally in a service cloud, giving aftersales staff a comprehensive picture of the products in use by customers and the needs of users.
The seven most important advantages of a service cloud
The following overview summarizes the most important advantages offered by a cloud platform for service in mechanical and plant engineering:
- Initial investments for cloud solutions are still manageable. A cloud platform for service also requires less effort for hardware and software maintenance compared to on-premise solutions.
- Cloud software can be expanded on a modular basis without companies having to invest their own IT resources. More storage space or more licenses can be added at any time and without any additional effort. In other words, the software scales in line with demand.
- If you want to develop new business models and generate additional revenue, you need to be able to adapt to trends such as artificial intelligence and big data as quickly as possible. A cloud platform provides easy access to new data-based technologies that are essential for building smart services in mechanical engineering.
- Cloud software does not become obsolete; it always remains up to date, thanks to regular updates by its provider. This is an important factor, especially with regard to cybersecurity and data protection. The updates protect against potential attacks and ensure that the software complies with current data protection regulations.
- In a cloud platform for service, information about spare parts and performed maintenance can be easily consolidated. This is because modern software offers interfaces to companies' existing tool landscapes.
- Cloud software is browser-based. This facilitates location-independent collaboration between aftersales employees and other company departments, as well as between service employees and customers.
- Getting started with the cloud is easier, especially for SMEs, than building their own hardware infrastructure and the tedious process of setting up servers and software. Even small teams are able to offer modern smart services to their employees and customers with a cloud platform.
A future-proof cloud solution for aftersales and service
With it's Quanos InfoTwin, Quanos has created a cloud platform that serves as a central database for modern services in machine and plant construction. InfoTwin intelligently links aftersales and service information, providing manufacturers and operators of machinery and equipment with valuable insights into the condition of their assets.
Quanos InfoTwin combines all the advantages of modern cloud solutions with a high level of data security and the know-how gained from over 1,000 customer projects. Companies in the mechanical and plant engineering sector can thus enter the world of digital spare parts information and technical documentation without any detours and secure time and cost advantages in the areas of maintenance, repair, and operation. Stay tuned and read on: Click here for Part 2 of our three-part blog series on the Quanos InfoTwin.