Efficient Service Planning in Mechanical Engineering: A Guide
In the complex and technology-driven world of engineering, service planning is a critical factor that makes a significant contribution to a company's efficiency and performance. The success of an organization is highly dependent on its ability to respond quickly to customer requirements, minimize downtime and optimize overall operational performance. This is precisely where service planning plays a crucial role.
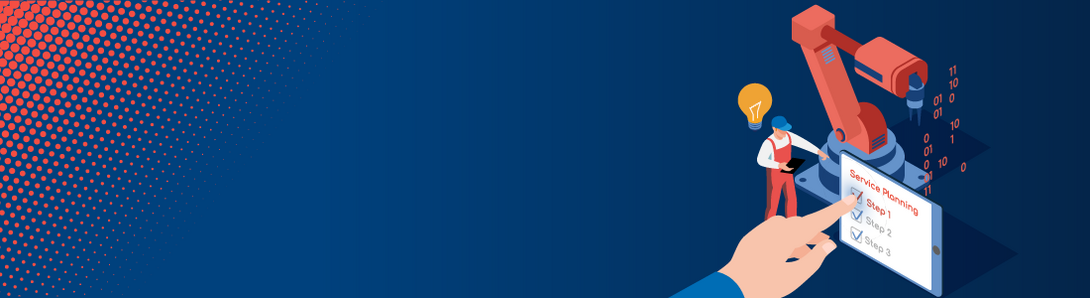
For a service employee in mechanical engineering, every day is a new challenge. Unpredictable machine breakdowns, logistical hurdles, safety requirements and compliance with standards and regulations are just some of the problems they face every day. So how can you ensure efficient service planning to meet these challenges?
Proactive maintenance and planning
The first step to more efficient service planning is to be proactive. Instead of reacting to problems as they occur, implementing predictive tools and predictive maintenance programs enables you to predict and prevent potential failures. This means that service teams can move from reactive to predictive working, which results in significant improvements in productivity and efficiency.
Effective planning and processes
Creating effective planning and process structures is another crucial factor for successful service planning. A well-designed and implemented process structure ensures that every step of the service chain, from initial customer contact to successful resolution of the problem, runs efficiently and effectively. A clear definition of roles and responsibilities within the team can help avoid overlaps and bottlenecks and improve workflows.
Digital transformation in mechanical engineering
Digitization offers a wealth of opportunities to improve service planning and execution. The use of digital technologies can automate processes, improve communication, and enable smoother and more efficient service delivery. Implementing technologies such as IoT (Internet of Things), AI (Artificial Intelligence) and digital twins can improve preventive maintenance and greatly enhance the ability of service personnel to identify and fix potential problems.
Risk management in service planning
Efficient service planning should also include sound risk management. Risks can arise from a variety of sources, including unpredictable machine breakdowns, supply chain disruptions or insufficient human resources. Identifying potential risks and developing strategies to mitigate them can improve service planning and optimize operational performance.
Service planning and customer relations
Finally, it should not be forgotten that service planning also plays an essential role in maintaining customer relationships. An efficient and smooth service process not only helps to minimize downtime and costs, but also increases customer satisfaction and loyalty. Therefore, improving service planning should always be seen in the context of improving customer relationships.
Conclusion: How to achieve efficient service planning
The road to efficient service planning in mechanical engineering is paved with challenges. However, it is precisely these challenges that offer opportunities for optimization and improvement. Whether it's implementing proactive maintenance programs, improving communication and coordination, or digitizing processes, each measure helps increase service efficiency and create a better customer experience.
With well thought-out spare parts management, supported by the use of digital spare parts catalogs and suitable software solutions, downtimes can be minimized and operations optimized. This not only ensures a more efficient service process, but also stronger customer loyalty and satisfaction.
Overall, the key to successful service planning is to see challenges as opportunities and to continuously look for ways to improve. Because in the dynamic world of mechanical engineering, standing still is not an option.