Our Vision
We help people understand machines
In all our software products, projects and ideas, we have one big goal in mind: helping people understand machines. And this understanding goes far beyond producing a simple operating manual or pushing the right buttons.
We want our customers to be able to query the status quo of an individual machine or system at any time and from anywhere - of exactly THIS machine.
- What was the condition at the time of delivery?
- How does the machine work and how do you put it into operation?
- What changes have been made since then?
- What is the condition of the machine - right now?
- When is the next maintenance due?
- Which spare part needs to be replaced soon and how does the repair work?
- How, where and how quickly can this spare part be obtained?
Integrated information management of digitally networked devices, machines and systems
To digitally map all individual information that answers such and other questions in a common environment at a central location, from technical documentation to service information to spare parts lists.
The digital networking of all this information creates a veritable knowledge environment for each individual machine and helps specialists to find exactly the information they are looking for as quickly as possible.
With this goal in mind, Quanos offers efficient solutions for the creation, networking and distribution of smart information for aftersales and service.

More time, less costs
Our solutions give you immediate access to all the information you need. This saves you valuable time when servicing - for example, when accessing product-related documentation, fault diagnoses, or identifying and ordering the necessary spare part. In addition, you avoid costly mistakes, for example due to incorrect stocking, double trips, unplanned service times and much more.

More Turnover
Our software provides you with information on availability, delivery times and costs in seconds. This simplifies the ordering process and shortens the time required for service technicians enormously. The direct and worldwide access of your service organisation to this valuable service and aftersales information, internally as well as externally, helps to increase your service turnover. Win-win for everyone.

New Business models
The purpose of our software products is to collect all valuable information about the use and condition of your machinery and equipment in one common place. Central data collection is the basis for innovative business and billing models. This is how Smart Services (digital value-added services) are created in your company - for more customer satisfaction.

Optimise competitiveness & service KPIs
Always one step ahead: Smart processes and transparent information improve response times and at the same time shorten processing times in the case of service. Customer-centric offers based on clear service information thus ensure you are more competitive. Just like the improved first-time fix rate and remote fix rate, which reduce unnecessary downtimes.
Smart information
What does that mean?
Whether in mechanical and plant engineering, the automotive industry, medical technology, aviation or energy technology: highly complex machines and plants are used for very specific tasks in every industry today. However, production and commissioning are not the end of the story: maintenance, repairs, conversion, dismantling and ultimately disposal follow.
During all these steps, digital information that can be called up at a central point gives all users or service staff a detailed overview of the respective machine (= Digital Information Twin). In the case of repairs, for example, this helps to find the affected spare part as quickly as possible, order it, replace it and put the machine back into operation as quickly as possible.
Digital Information Twin
Digitalisation is turning our world upside down in almost all areas. Not only products are becoming smart, but also their creation. Digital data is created during design and production, but also during use, and is available to all process participants throughout the entire product life cycle. A digital twin is created.
The connection of all information belonging to the product enables new business models, which in turn require new forms of product support. The Digital Information Twin is the basis for the highest possible availability of products and efficient service.
Quanos provides the software tools that help create the Digital Information Twin.
Smart maintenance
It used to be that if a machine had an error message or even a breakdown, the service technician was called to solve the acute problem - sometimes with more, sometimes with less downtime.
A revolution is underway in the area of maintenance and service: with the feedback that IoT technologies enable from the machine back to the upstream processes, not only does valuable information get back there, but completely new service and business models also become possible.
Depending on the degree of digitalisation, networking and intelligence of the available data and information, everything seems possible: from the operational maintenance of individual machines to intelligent predictive maintenance to reality-based maintenance of an entire machine fleet. How these next steps on the way to smart service and intelligent maintenance look like is presented in our white paper.
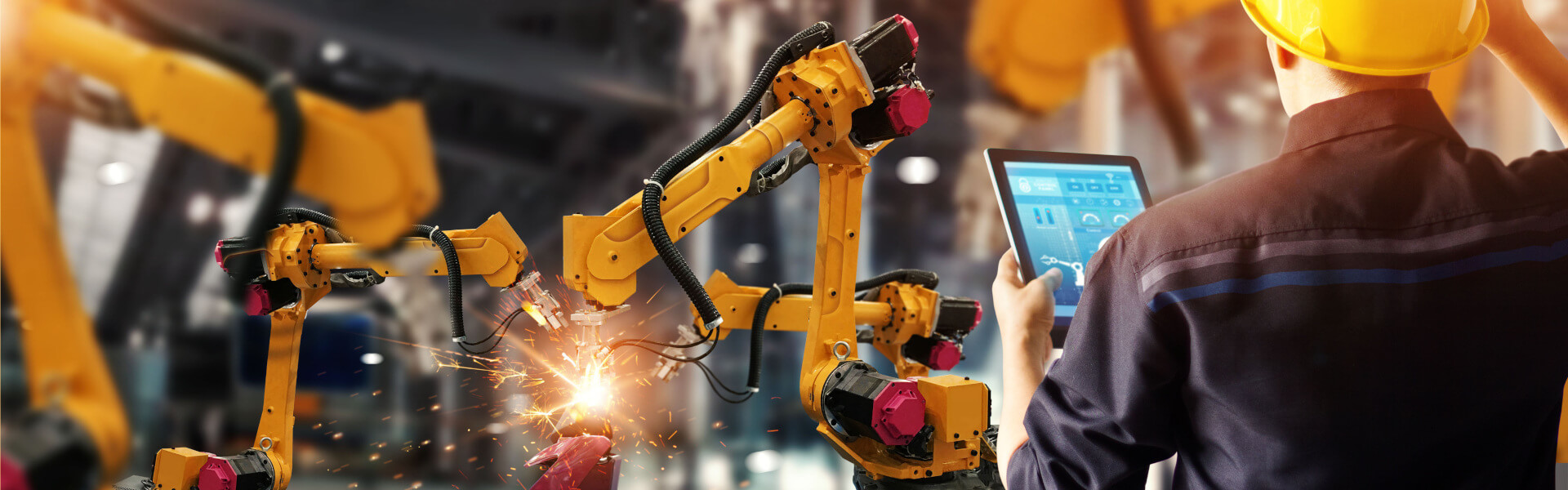
Our mission
Our goal is to help people understand machines. High-quality, digital information is the basis for this and intelligent networking is the logical consequence. With our software products, we are setting the course for precisely this. Our claim is to offer the world's most powerful and user-friendly platform for integrated information management of digitally networked devices, machines and plants.
Our team of around 300 experts works hard every day to provide our customers with the best solutions for their editorial, after-sales and service processes.