Due to digitalization and globalization, technical writing has a key role to play these days. At the same time, it must keep developing in its own right, to meet the requirements of its demanding target groups.
Technical writers do more than just convey knowledge: they are service providers who have the responsibility of conveying complex information correctly and comprehensibly.
By delivering efficient documentation, they aim to save users time, without giving themselves more work to do in preparing information. To achieve this, they face major challenges.
Technical documentation must:
- Make extensive technical information available quickly, easily, and without difficulty
- Provide comprehensive information about all available documents on a specific topic
- Convey the information that experts and less experienced users need
- Make it possible to filter information as required
- Automatically link information from different sources
- Be adaptable to international markets
- Communicate all required and current safety regulations
- Adapt to new tools and technologies
Content delivery systems already help technical writers with many of these challenges. But particularly when it comes to networking information, they soon reach their limits, requiring plenty of manual interventions and rework.
A digital information twin applies the benefits of content delivery systems to a networked, digital environment enhanced with intelligent functions. This enables you to make technical documentation available in digital formats and to increase user satisfaction.
A digital information twin (DIT) stores technical information and service information about a product, machine, or plant. The DIT forms a central data platform that bundles and synchronizes information.
The result is an integrated information management system that helps service engineers be more productive. Technical writers also get a connected content delivery system that goes beyond the conventional content delivery principle.
Efficiency benefits for machinery and plant construction
A DIT brings various efficiency benefits to the day-to-day work of technical writers, and to all those accustomed to working with technical documentation:
- Spare parts information and maintenance instructions are found more quickly by DIT users such as service engineers or maintenance staff.
- An intuitive user interface takes DIT users directly to the relevant information for their maintenance tasks.
- All the technical information is accessible quickly and digitally in one place.
- All users, including partners and customers at home and abroad, are given customized access to the information – at any time, 24/7.
- Technical writers can make bundled adjustments to documentation, and updates can be automatically delivered to all machine locations.
See for yourself
Videos contain English subtitles
Benefit from a connected content delivery system and combine technical information and data to a digital twin. Everything you need is in Quanos InfoTwin.
Along with cleverly designed functions, the intuitive user interface of Quanos InfoTwin makes the work of technical writers easier – around the world, around the clock, and on any device.
Quanos InfoTwin is
- the standardized cloud solution from Quanos for technical writing in mechanical and plant engineering.
- an aftersales platform that is ready to be used immediately, and which can be expanded on a modular basis at any time.
- a modern platform that aggregates the aftersales information and the technical documentation to a digital information twin, and networks them intelligently.
- the basis for new business models and smart services.
- a functional networking tool for the entire aftersales area.
- an information and documentation system that offers an asset-based overview of individual products, thereby putting the focus on their status.
For more productive working with technical documentation
Quanos InfoTwin combines information from different data sources, and makes it available over an intuitive interface. Find out what this means in detail for the quality of your technical documentation.
With DIT from Quanos, productivity is boosted for you and your users. The cloud-based Quanos InfoTwin is available around the world and around the clock on any device – no matter whether the user is working at a customer’s plant directly on site, or looking for information in the office.
Documentation & Knowledge: A functional package specifically for technical documentation
Quanos InfoTwin has been developed for aftersales & service, and networks information from technical documentation, spare parts management, and other sources.
The platform offers different capabilities for different stakeholders. The “Documentation & Knowledge” capability is provided specifically for technical writers. This enables you to process information in a new way:
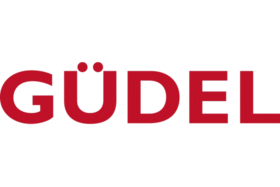
„The plan to set up a single source of documentation was a complete success and we were able to move past the data silos and the inefficiencies that came with them. The QR code on their Güdel product provides our customers with a direct, digital means of accessing the technical documentation.“
Güdel Group AG Jürgen Stitz, Documentation Manager, Güdel AG
Sounds interesting?
Quanos InfoTwin Capabilities: Catalysts for your success
Quanos InfoTwin networks information from technical documentation, spare parts management systems, and other sources. Get to know the capabilities for increasing productivity and efficiency offered as standard by Quanos InfoTwin.
By combining technical documentation and Quanos InfoTwin, create new services and increase your turnover with modern business models. The following examples are just the start – your options are endless:
- Information systems for service teams or for your staff: Share your latest service documentation to suit the different target groups. One of the possible benefits here is the monetization of chargeable content.
- Content Application Integration: Integrate technical information into your own apps and portals. The TwinAPI of Quanos InfoTwin makes it possible to embed SCHEMA ST4 content into other information services and company portals, or to set up or improve company-specific apps.
- Central documentation portal: Create a central point of contact on the internet where all the technical documentation is available. Flexible access rules ensure that parts of the technical documentation are only available to selected users.
- Online software help: With Quanos InfoTwin, you establish context-sensitive and online-based help systems for software applications. Add FAQs, guidelines, or knowledge articles to your Help Center that are always up to date.
Benefits for technical writers
- Combine technical documentation with relevant service information, so that your users achieve the best results.
- Centralize all the technical documentation information and maintain an overview.
- Take your technical documentation to every device.
- Only work with up-to-date, correct, and networked information.
- Integrate Quanos InfoTwin into your most important tools and improve the flow of information.
- Like your users, navigate more quickly through the technical documentation, and save time looking for information.
Process with a content delivery system
- Information from ERP systems, catalog systems, or CCMSs are stored in HTML or PDF format in the content delivery system
- Data can be delivered in a target-group-oriented manner – but there is no overview of the additional information in the complete technical documentation collection
- Search functions create a complete overview, but do not allow information to be linked
- Documents can only be connected in an editorial way, which requires a great deal of effort
Process with Quanos InfoTwin
- Aftersales and service information from different sources is linked fully automatically
- The process is controlled via a common metadata system – manual interventions by technical writers are no longer necessary
- Each document “knows” that it is relevant for a specific product, a specific product line, or a specific target market
- Users navigate intuitively from source to source, and bring all the information relevant to their task from the depths of the system to the user interface