Sparked interest?
Güdel Group AG
A Central Location for Technical Documentation: Headless Content Delivery Finally Gets Everything Flowing
Swiss company Güdel specializes in industrial automation and flowing processes. The manufacturer was looking for a central platform to also ensure a smooth flow of information in its technical documentation—and found the right solution at Quanos.
Güdel Group: moving products for automation
Güdel has been setting industrial automation in motion for seven decades. Headquartered in Langenthal, Switzerland, the family business and its team of around 1,000 employees develop intelligent technologies aimed at automating and optimizing industrial processes.
Originally starting out as a manufacturer of rack and pinion components, the company's portfolio now includes linear guides, gearboxes, traversing axes for robots, gantry systems, and press lines. Güdel also develops custom solutions to meet special customer requirements.
The Swiss company’s extensive portfolio of products sets automation technology in motion with the aim of minimizing downtime and frictional losses while enabling flowing, reliable, and efficient production processes for plant operators.
Challenges: five locations, five documentation processes
But while Güdel excelled at getting its customers’ processes flowing, the company’s own processes in its technical documentation department had ground to a standstill. The company has technical writing teams at five locations in different time zones that provide technicians and customers with all the information they need on machines and components. But the teams weren’t storing data in a centralized location and struggled due to the time difference and a lack of personnel, which led to data silos, outdated data, and inefficiency.
Jürgen Stitz, Documentation Manager at Güdel AG, describes the issues this caused: “Our technical writing teams would sometimes create several instances of the same information, and we were unable to reuse or evolve our content.” The technical writing teams at the different locations didn’t have a clear overview of the content, and this slowly but surely became a serious problem.
“In Langenthal, we have a well-structured archive with PDF files dating back to 2007. This legacy data is invaluable for our customers and service team,” Stitz says, adding: “Theoretically speaking, it shouldn’t take long to make the data available - but when it came down to it, the lack of a centralized data storage location was often an issue. The technical writers at our headquarters in Langenthal alone spent around 200 hours every year looking for information and documents.”
Requirements and goals: single source of truth for the documentation
Güdel wanted to enhance the efficiency of its internal processes, so the company set itself the goal of making existing and newly generated documentation - which is currently in PDF format and will eventually include HTML as well - centrally available on one platform so it can be accessed around the clock.
Güdel had already laid the groundwork for this step back in 2021 and has since been equipping its products with a QR code that grants users access to the technical documentation. This gave the platform the company was planning a key advantage: “In 30 to 40 percent of cases, we don’t even know where our machines are located once they’ve been integrated into a larger plant,” Stitz notes. End customers can use the QR code to register and obtain service information, and this also gives Güdel better data on the location and use of its products.
Based on this information, the service team can offer end customers tailored services and contracts. One key aspect here is the system for assigning permissions, which has to work properly to ensure customers can only see the information intended for them.
Güdel’s plan was to create a single source of truth that links order-related data from SAP with the technical documentation. Automating the generation of metadata to the greatest possible extent was an important part of this. The company also wanted documents resulting from the linking of order-related SAP data with technical documentation to then be seamlessly accessible in other systems as well.
Solution and implementation: a headless InfoTwin paves the way for the future of networked documentation
Güdel opted to work with the experts at Quanos as their software partner for the project. Initially delayed due to the pandemic, the project got back on track again in 2022 when management announced the company was going on a digitalization offensive. Jürgen Stitz’s department was the first to get the go-ahead as it had presented the most convincing digitalization concept.
Just two years later, in April 2024, the myDocuments application went live on the myGüdel customer platform - and Stitz and his team achieved the goals they had set for themselves. The myDocuments application is based on Quanos InfoTwin, which functions as a headless content delivery system in the background upon which Güdel can support its own applications.
Quanos used a spooler that forms part of InfoTwin to set up a data transfer from the fileshare software Güdel was previously using so existing information could also be incorporated in the technical documentation portal. The program matches metadata from SAP with PDFs from Güdel’s document archive.
First off, the partners transferred around 60,000 documents via the spooler and then used tests to gain feedback from the system’s future users at headquarters and in other countries. “Tim Rausch, who is a customer success manager at Quanos, was a great help here together with his team,” says Stitz, commending the partners’ collaboration. “By combining our efforts, we have now transferred more than 100,000 documents to the new platform.”
Customers who want to access the documents need only scan the QR code on their machine’s rating plate and log in to myGüdel. The portal sends InfoTwin a request for the information via the myDocuments application, which pools all the instructions relating to a machine, and the information is then provided to the customer as a PDF in myGüdel.
Result: a great help for technicians, technical writers, and customers
There has been a sharp decrease in requests for subsequent copies of documents since myGüdel was introduced and the company’s documentation processes were automated—which means the technical writing teams and service staff at Güdel’s five locations can now carry out their own searches regardless of the time difference and who is working that day.
“The plan to set up a single source of documentation was a complete success and we were able to move past the data silos and the inefficiencies that came with them,” says Stitz.
He explains: “Documents from InfoTwin can now be retrieved via systems such as Salesforce. The QR code on their Güdel product provides our customers with a direct, digital means of accessing the technical documentation.” This system also means that the Swiss manufacturer is already ideally equipped to meet the requirements of the EU Machinery Regulation, which will officially authorize manufacturers to supply customer documentation in digital form from 2027.
“The implementation of myGüdel with support from Quanos went so well that other departments have already expressed an interest and are now looking for a solution based on InfoTwin for their own documents and information,” summarizes Stitz.
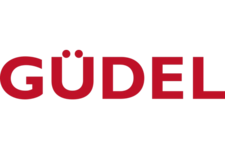
Güdel Group AG
„The plan to set up a single source of documentation was a complete success and we were able to move past the data silos and the inefficiencies that came with them.“
Mechanical and plant engineering