Bringing Innovation to Rail Transport with Reliable Spare Parts Service
Business with new rail vehicles is losing momentum. That's why representatives of the rail industry must now put all their eggs in the service basket. Aftersales offers the opportunity to master the most important challenges related to the railways and to set the course for the future.
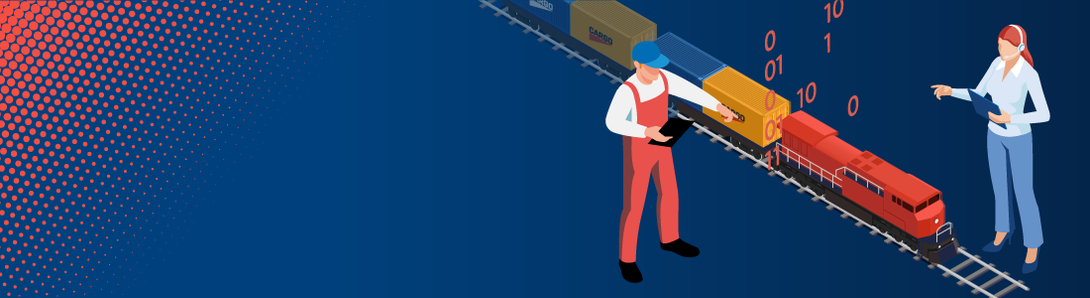
An industry gets people and goods rolling
The rail industry in Germany is a beacon of hope for green mobility and a major employer. In addition to the employees of many rail transport companies such as Deutsche Bahn, around 56,600 employees at system providers and medium-sized suppliers are keeping rail transport rolling.
Companies in this industry, many of which are organized in the German Railway Industry Association (Verband der Bahnindustrie in Deutschland e.V. or VDB), perform a wide range of tasks. Besides the production of systems and components for rail vehicles, this includes track construction, the manufacture of engines and transmissions, and important services related to maintenance and spare parts.
The rail industry is facing these challenges
Thanks to their high technical level, the products of the rail industry make an important contribution to sustainable mobility in passenger and freight transport in Germany and worldwide. However, the road to a green and competitive future is paved with challenges.
Back in 2016, the Hans Böckler Foundation conducted a comprehensive analysis that took an in-depth look at the key hurdles the rail industry was facing.
- Poor infrastructure: According to an internal report by Deutsche Bahn, 26 percent of all switches are in poor, defective or inadequate condition, as are 48 percent of all signal boxes. As a result, only 75 percent of all trains arrive on time — which means with a delay of less than six minutes. In long-distance traffic, that figure is often only 60 percent. The poor condition of the infrastructure makes rail operations more difficult.
- An investment backlog: Investments are needed for improvements to the rail network. The German government wants to provide a total of €45 billion by 2027. But only a fraction of this amount is earmarked for 2024 in the draft budget. "Without a long-term funding outlook, the industry will not invest in building capacities, resources, and the necessary fleet," warned VDB Chief Executive Sarah Stark in an interview.
- Global competition: With an export ratio of over 40 percent, the German rail industry is an important driver of modern mobility worldwide. However, competition from Asia and other parts of the world is growing. For example, global export markets have become increasingly important for Chinese manufacturers in recent years.
- A shortage of skilled workers: The changing world of work and the aging of society are making it more difficult for companies to find young talent. They must therefore position themselves as attractive employers and introduce more efficiency into their recruiting processes in order to compensate for the skills gap.
- High costs: Rising costs are putting pressure on the rail industry. The drivers of this pressure include infrastructure, vehicle, and energy costs. Companies need solutions that enable them to provide and use their infrastructure as efficiently as possible. Digitization plays a major role in this area. The basis for this digitization is the standardized European Train Control System (ETCS) — but its expansion is progressing only slowly.
- Sustainability: Through digitization, the rail industry can not only save costs but also make a significant contribution to climate protection. According to the VDB, digitization in the rail industry could cover almost half of the emissions reduction in mobility that is demanded by the German government.
What role do aftersales and maintenance play in overcoming the hurdles?
In recent years, the German rail vehicle market has experienced major slumps, especially in the important market segments for locomotives and railcars. According to the VDB, the level of sales in 2022 was 16.7 percent higher than in 2021. At the same time, however, order intake fell by 18.5 percent.
For this reason, and because the rail industry will have to focus on its own modernization and maintenance in the coming years, the importance of aftersales in the rail industry is increasing. Owners and operators are focusing more on the cost, quality, and efficiency of rail technology products throughout their entire life cycle.
Digitization is the key
According to an analysis by the Hans Böckler Foundation, expanding the service business is "currently the most important strategic option for manufacturers to extend the value chain." The longer the value chain, the longer the aftersales department must ensure the availability of spare parts.
In addition, for efficient maintenance, the identification of required spare parts must be made as simple as possible — because rail vehicles and components are becoming increasingly complex.
A Roland Berger study from 2016 concluded that rail companies can overcome these and other challenges with the help of digitization. According to the study, "operators should improve their products and services while reducing their operating costs, including for maintenance and repair."
In 2016, when the study was published, European operators spent more than €16 billion annually on maintenance and repair. According to Roland Berger, digitization of these areas enables savings of 20 percent by means of longer and more flexible maintenance intervals and shorter downtimes, among other things. The VDB even estimates savings of 30 percent.
However, many companies lack the know-how that is required for measures such as evaluating existing data and optimizing their component maintenance cycles.
A strategy for stability: Optimizing service for rail products
Railroad industry companies that want to position themselves for the future must set their course now and transform their aftersales. If this task is also on your agenda, you should
- provide excellent service to cushion the fluctuations in new vehicle business
- enable your customers to make quick repairs to keep downtime and costs low
- ensure that replacement part identification is as simple and correct as possible
- implement modern approaches such as predictive maintenance
- improve your service processes to reduce the workload of aftersales employees
The Roland Berger study also suggests focusing on "coopetition" — that is, cooperation with the competition in the areas of maintenance and repair. This makes it possible to more accurately identify technical faults and wear and tear, and to fully exploit the potential of data. It’s also important to keep an eye on the entire value chain, from materials monitoring and maintenance planning to operational activities in the operating plant.
All aboard, please: A digital twin with service data and technical documentation
The easiest way to digitize your service sustainably is to use the right software. Quanos InfoTwin provides the rail industry with a ready-to-use tool: a cloud-based platform that creates a digital twin for your aftersales and forms the core of your service transformation.
The solution is modular — you can first structure your aftersales data and then gradually network it with technical documentation, spare parts management, and other sources in a service portal.
As a result, your aftersales team experiences a noticeable gain in efficiency in their day-to-day work and is able to provide your customers with the best possible support. In turn, customers benefit from greater transparency when identifying spare parts and planning maintenance.
VOITH Lokomotivtechnik is an example of how a locomotive design company uses software to offer its customers first-class service and optimal support for vehicles, and of the advantages resulting from the combination of technical documentation and aftersales.
You too can score points with optimal processes in aftersales. Get to know Quanos InfoTwin in a free online demo. We’ll be happy to show you how the platform can help you master your acute challenges.