Looking for New Business Models? Implement ‘Operator Models’ and More with Digital Twins
The expression "a rolling stone gathers no moss" has never been more relevant than it is today. If machine and plant manufacturers want to remain competitive, they must develop new business models. Learn why manufacturers should not be left behind and how your company can move into the digital fast lane.
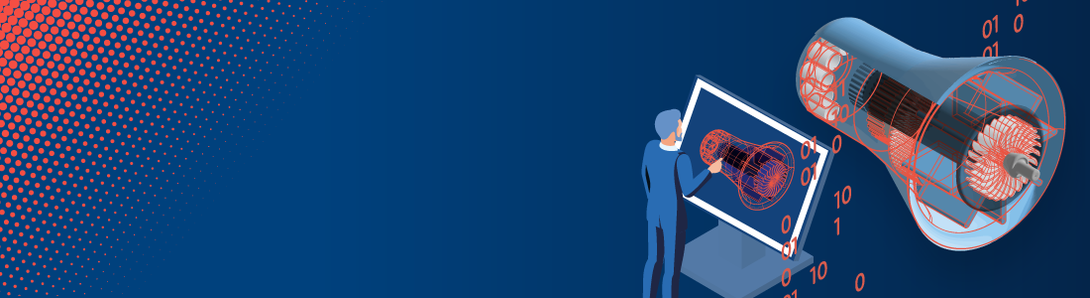
German companies are lagging behind in the digital world
In 2019, the digital association Bitkom asked German industrial companies whether digitization was affecting their business model. 65 percent of respondents agreed. Bitkom President Achim Berg said at the time: "We can see quite clearly that the real revolution of Industry 4.0 is not taking place in production alone, but in business models. That's why every company should put its business model to the digital test."
What keeps machine builders from taking off digitally?
In a joint publication, the VDMA and McKinsey consultants have examined obstacles and challenges in implementing digital business models:
- Machinery and plant manufacturers lack technical and management know-how.
- Companies fear the loss of data or see their data integrity at risk.
- Those who already offer business models based on digital platforms are nevertheless missing opportunities due to a lack of data monetization.
The study also shows that operator models such as "pay per use" are not yet on the agenda of many machine and plant manufacturers. This may be because they see no need for them or because their existing business models still work. However, this is too short-sighted.
This is why mechanical engineering needs new business models
Companies have to adapt ever faster to new customer and market needs. In addition to customer centricity, digital business models are indispensable for this. Those who succeed in digitizing products and services actively shape the market and increase their competitive edge.
This does not mean that industrial companies have to swap engineers for developers. It is much more a matter of dovetailing the product world more closely with digital technologies. Tools, machines and spare parts remain important assets. What is changing is the focus:
- Sales are taking a back seat, while machine use and yield are becoming new sources of revenue.
- The better a machine builder's machine performs, the higher the yield.
- In addition to black figures, companies benefit from data that serves as the basis for new business models. This allows smart services such as predictive maintenance to be established and perfected.
New business models also enable machinery and plant manufacturers to position themselves as pioneers in the field of sustainability. On the one hand, they can increase their sales and, on the other, assume social responsibility. This view is also shared by “Plattform Industrie 4.0” in a discussion paper on Industry 4.0 and sustainability.
Example: The operator model for mechanical and plant engineering
The operator model already shows what a digital business model for machine builders can look like. It is no longer based on the sale of machines, plants and equipment, but on the sale of the output.
Producers no longer invest in the purchase of a new machine, but in its output. In the case of an air compressor, for example, that's the amount of air compressed.
Advantages for machine builders:
- Long-term customer loyalty
- Acquisition of data for product improvement and development of further services
- Sales depend on performance, not on the number of machines sold
Benefits for plant operators:
- Capital investment shifts from CapEx to OpEx
- Maintenance and servicing are taken over by the machine builder
- Plannable costs
We summarize further examples for you in our blog article on the subject of Smart Services.
Goals of digital business models
With digital business models, machinery and plant manufacturers offer their customers an incentive to use their services in the long term. According to the VDMA survey, the companies themselves are hoping for the following benefits:
- Optimization of the use of resources
- Improvement of plant output and overall equipment effectiveness (OEE)
- Improvements in service, after-sales and maintenance
- Increased flexibility in plant utilization
How industrial companies implement new business models
In order for manufacturers to build and further develop digital business models, they need to have an overview of their machines and service information at all times. The necessary transparency and networking are provided by data generated during operation, maintenance, and repair.
Machine builders therefore need a knowledge base around their products and service processes. Digital twins provide the necessary infrastructure for this: They bundle information centrally and in real time and create a virtual representation of spare parts, devices and systems - a Digital Information Twin.
Maintenance on the physical machine is also stored in the master data of the digital twin and is available centrally and always up to date. This creates a digital lifecycle for plants and components.
Benefits for machine builders and their customers:
- Easy establishment of new sales channels for spare parts, tools, or services
- Continuous improvement of service KPIs
- Bidirectional linking of service information and documentation on wear and spare parts
- Optimized information transfer between departments and with customers
- Comprehensive data on customer satisfaction, machine performance, maintenance, and servicing
- Solid basis for self-service portals
- Increased customer loyalty
Your entry into the world of digital twins: Quanos InfoTwin
With Quanos InfoTwin, digital twins for the industry are already coming to life today, securely and without high IT effort. The cloud solution combines information from after-sales and service with product information and makes it available to customers and employees in an intuitive web interface.
Service documentation is distributed precisely and securely to a defined target group. On the one hand, this increases the trust of users and, on the other, it simplifies monetization, as content can be offered for a fee if desired.
Manufacturers and operators use InfoTwin to represent their machines and systems that are in the field. For data transfer, the platform offers modern API interfaces to common tools such as CAD, ERP or PLM. Companies therefore do not have to fear that their IT resources will be blocked for days due to the introduction of the digital twin.
The cloud software is constantly being developed further and is automatically up to date. In addition, the modular InfoTwin can be used to gradually implement further Smart Services starting from spare parts information and technical documentation - depending on how requirements change in the company or among customers.
This is how machine builders are proceeding now
If your company is ready for new business models and you want to take your service to the next level, Quanos experts have years of experience to help.
Important questions companies typically have around the Quanos InfoTwin are answered in a free online demo. Take a look at the benefits of digital twins now.