Maintenance Management in Mechanical Engineering: 5 Tips for Maximum Cost Efficiency
In today's competitive mechanical engineering industry, it is critical to develop maintenance management strategies that both maximize asset availability and minimize costs. In this blog article, we will share five breakthrough approaches to help you implement effective maintenance management in mechanical engineering.
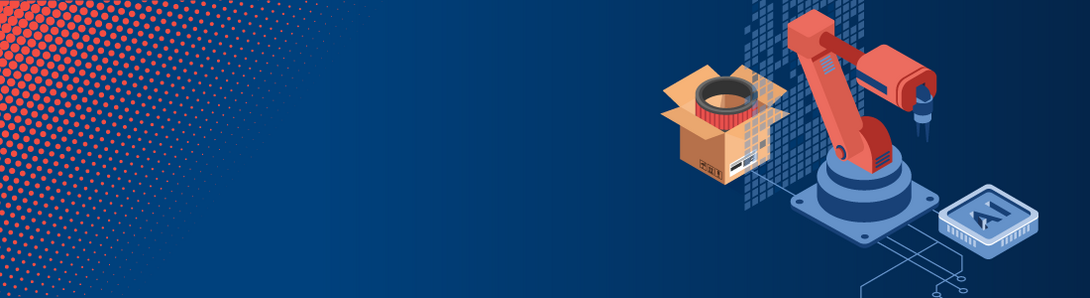
1. Implementation of condition-based maintenance
Condition-based maintenance incorporates the current condition of the machines into maintenance decisions. Instead of insisting on fixed maintenance intervals, maintenance measures are only carried out when the machine's condition requires it. Continuous monitoring of machine data and using modern sensor technology allows you to determine the optimum time for maintenance work, enabling you to use resources more efficiently and save costs.
2. Predictive maintenance
Going one step further, predictive maintenance is an approach that uses real-time data and predictive analytics to forecast potential machine failures before they occur. By using sensors and IoT technologies, you can continuously monitor the condition of your machines and take early action to prevent failures and unplanned downtime. This leads to improved plant availability and a reduction in maintenance costs.
3. Data analytics and artificial intelligence
Data analytics and artificial intelligence (AI) can have a significant impact on maintenance management. By using AI and machine learning, you can identify patterns in machine data that indicate potential problems or inefficiencies. This allows you to be proactive and extend the life of your machines. In addition, data analysis enables better planning and control of your maintenance activities, resulting in cost savings and improved asset availability.
4. Training and continuing education of maintenance employees
The competence of your maintenance staff is a key factor in the success of your maintenance management. Invest in training and education to ensure that your employees have the latest knowledge of mechanical engineering, maintenance techniques and technologies. This not only helps improve maintenance performance, but also increases employee satisfaction and motivation.
5. Standardization and optimization of maintenance processes
Standardizing and optimizing maintenance processes is crucial for effective maintenance management. By introducing clear procedures and processes for the maintenance and repair of machines, you ensure that all employees work to the same standards. This minimizes the risk of errors and improves the efficiency of your maintenance operations. Use digital tools and modern software solutions to further optimize your maintenance processes and promote collaboration between different departments.
All information for maintenance in one system
A modern spare parts and service information system such as Quanos SIS.one brings together all relevant service information about technical equipment and systems. Via an intuitive user interface, information on spare and wear parts as well as the associated technical documentation such as maintenance instructions, repair instructions, electronic schematics or parts lists, labor values and stock levels are available to the user.
Thanks to well thought-out search functions, maintenance technicians save a lot of time when searching for information - which ultimately reduces machine or plant downtimes.
How does this benefit you as a plant operator or manufacturing company? Read more about this in our blog article.
Would you like to experience for yourself how easy it is to find the spare parts you need and the relevant information for carrying out maintenance work in Quanos SIS.one?