Cost Optimization in Machine Maintenance: 4 Effective Approaches
In machine maintenance, cost efficiency and the quality of the work performed are critical to a company's success. In this blog post, we examine four effective strategies for cost optimization in machine maintenance that can be applied by maintenance managers and technical service managers in mechanical engineering.
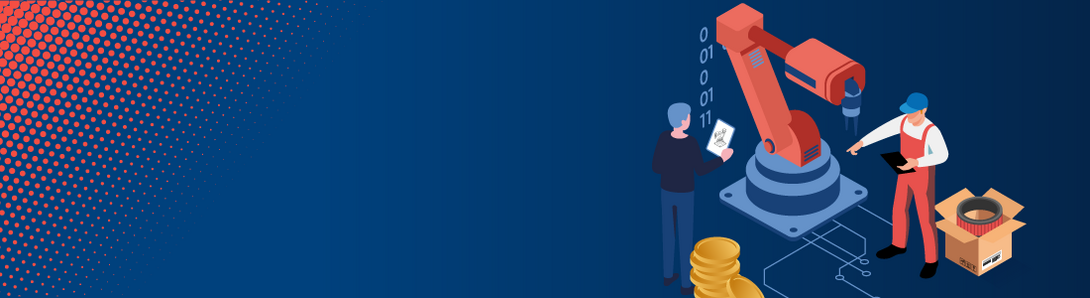
1. Planning and organization of maintenance measures
Well-structured planning and organization of maintenance activities is essential for successful cost optimization. By drawing up maintenance plans and regularly reviewing them, maintenance managers can ensure that the required resources are deployed efficiently, and potential bottlenecks are identified at an early stage. In addition, structured planning enables maintenance work to be carried out at times of lower capacity utilization, thus minimizing the impact of machine downtime.
2. Proactive maintenance and predictive maintenance
Switching from reactive to proactive maintenance is a crucial step towards cost optimization in machine maintenance. By using condition monitoring technologies and predictive maintenance, maintenance managers can identify potential problems at an early stage and initiate maintenance measures in a targeted manner before major damage or failures occur. This helps to reduce unplanned downtime and associated costs.
3. Use of data analysis for continuous improvement
The use of data analysis tools and methods to continuously improve maintenance processes contributes significantly to cost optimization. By collecting and analyzing machine data, maintenance reports and key performance indicators, maintenance managers can identify weak points that cause avoidable repair and maintenance costs. The insights gained make it possible to initiate targeted measures to improve maintenance processes and thus increase efficiency and reduce costs.
4. Optimization of spare parts logistics
Efficient spare parts logistics is an essential factor for cost optimization in machine maintenance. The availability of spare parts, the minimization of delivery times and the reduction of unnecessary inventories are crucial aspects that support the maintenance manager in controlling maintenance costs. By using digital spare parts catalogs and modern inventory management systems, service managers can optimize the ordering and procurement process and thus save costs.
All information for maintenance in one system
In a modern service information system like Quanos SIS.one, all the necessary information for maintenance is bundled. Here, spare parts information, 2D and 3D drawings, links to the corresponding location in the technical documentation, circuit diagrams, hydraulic diagrams and much more can be found. Thanks to sophisticated search functions, maintenance technicians save a lot of time searching for information. This in turn reduces machine downtime. When the information needed is available immediately and in a central location, on-site work can be completed more quickly. This saves considerable costs in machine maintenance.
Would you like to experience for yourself how you can easily find required spare parts and relevant maintenance information in Quanos SIS.one?