Efficient Interfaces in Mechanical Engineering: What Makes Them Essential?
For many industrial companies, protecting data and benefiting from it at the same time is something of a balancing act. Machine and plant manufacturers need compliance, the right mindset, and efficient interfaces to establish continuous data flows. Find out how data hubs and APIs can help you and your customers to benefit from machine and service data.
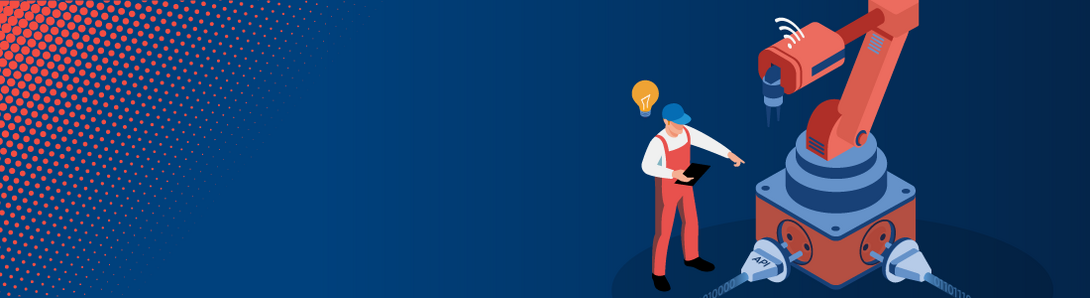
Networked data makes it easier for companies to optimize their processes and tap into new business opportunities. For many machine manufacturers, however, the consistent use of data across departmental boundaries is still a hope for the future. While sufficient data on spare parts, machines, customers, and service support exists, it is frequently trapped in isolated systems that do not communicate with each other. Interfaces can be used to overcome these hurdles.
So why are interfaces so important?
Be it in e-commerce, the healthcare sector, or industrial manufacturing, interfaces form the backbone of an efficient system landscape and are a prerequisite for digitization. They serve, for example, to enable machine and component manufacturers to smoothly manage data.
Specifically, interfaces ensure that machines, aftersales platforms, and systems such as ERP, PIM, and CRM can communicate seamlessly with each other and exchange data. By smoothly integrating their systems and data, machine manufacturers can:
- Automate their processes and reduce errors
- Manage and use their aftersales data more efficiently
- Optimize service callouts to customers
- Make data-based decisions during service and maintenance planning
- Enhance their service quality
- Provide accurate and up-to-date information for employees and customers
- Reduce data silos across the company
- Improve transparency in all company processes
- Develop new business models such as data-based services
Sorry, this number is unavailable; why data connections often fail
It has long been clear to machine manufacturers and their customers that interfaces are crucial to the success of digitization. Nevertheless, very few companies manage to network their data company-wide. The reasons for this lie partly in their technological DNA and partly in their processes.
Technological obstacles impeding functioning interfaces
In many companies, departments establish different system architectures and varying data structures over time. While tools are being modernized and further developed, the heterogeneous isolated solutions of individual departments never grow together to form a large whole.
Added to this, systems from different manufacturers often use data formats that are not compatible, which makes it difficult to import and export data, and to ensure interoperability between systems and their integration into modern, open interface architectures.
Organizational challenges facing networked data
If company departments want to share data, they not only need to be on the same wavelength technologically, they also need to develop a common mindset – because high quality and consistent data can only be achieved through close collaboration.
Networking projects also require that the parties demonstrate a willingness to transparently share data from their own “areas of sovereignty” with others. However, many managers and IT experts fear threats to compliance with GDPR provisions and information security, and see interfaces as potential gateways for cyberattacks, through which business secrets could fall into the wrong hands.
Best practices: what are the benefits of establishing interfaces for your company?
If machine manufacturers succeed in setting up continuous data streams with the help of interfaces, this results in important advantages for both internal processes and collaboration with customers:
- Interfaces are indispensable for predictive maintenance. Machine manufacturers and their customers can record machine data in real time and identify potential problems at an early stage. This allows them to plan maintenance work in good time.
- Interfaces in the spare parts shop ensure that up-to-date and correct information is displayed at all times. When ordering spare parts, users can quickly navigate to the part they need and be sure that it will be delivered on time. This is particularly helpful for sectors such as agriculture, where machine users depend on punctual and correct spare parts deliveries due to the seasonal nature of their industry.
- Shared service portals ensure that technicians and customers of machine manufacturers can find the right information on spare parts and instructions for efficient maintenance with just a few clicks.
The examples show that the benefits of networked data become greater as the number of departments and partners able to work with it grows. That is why interfaces should not only network internal company data, but also offer added value for customers and suppliers.
This creates an ecosystem of valuable information that improves your products and services and simplifies collaboration with other companies.
Strategies for establishing interfaces in the mechanical engineering sector
If you want to use interfaces successfully and in doing so improve aftersales service, for example, you need to take a strategic approach. The following steps will point you in the right direction and help you reach your goal.
Step 1: Analysis and planning
First of all, you need to consider what added value the data to be networked offers your company, your service team, and your customers, and you also need to define relevant use cases. You must then identify the systems in which important data is stored, and that are to be connected via interfaces. You also need to define clear integration goals and KPIs for structured data networking.
For example, one integration goal could be to enhance aftersales efficiency. Possible KPIs are the average response time to customer inquiries or the first-time fix rate, which should be reduced.
Step 2: Technological implementation
The second step is the technological implementation of the interfaces. Middleware and integration platforms will assist you with this. To make sure that data is able to flow seamlessly through your systems, it is advisable to create a higher-level data layer. This is used to collect and synchronize information and distribute it to departments and tools.
One suitable solution here is cloud platforms. With Application Programming Interfaces (APIs) and connectors, these platforms offer flexible and modular interfaces and can be scaled and expanded as required. Furthermore, they also enable users to encrypt data and clearly regulate who has access to which information.
Step 3: Start and work in an iterative manner
Don't waste time when networking – the competition never sleeps. Avoid spending too long on data optimization; instead use your interfaces to bring heterogeneous isolated data into a clean data flow throughout the entire company. Once you’ve established your data flow, you can continuously improve the data quality.
Important: Ideally, networking projects should be supported by the management team, while someone within your company should also assume a pioneering role in networking and pro-actively drive the digital transformation forward.
How machine manufacturers use APIs for efficient aftersales and service
The APIs of modern software solutions play a central role in digital projects. They connect systems and platforms for which no standard connectors exist, and ensure that system architectures can be expanded as and when required.
In machine and plant construction, APIs link data from sources such as machines, maintenance software, and ERP systems in real time and enable technicians to access up-to-date data on spare parts or repair instructions. You can use TwinAPI, for example, as an API for networking your data.
How does TwinAPI work?
TwinAPI is a flexible interface of Quanos InfoTwin – a central cloud platform for networking systems in aftersales, technical documentation, and beyond.
The programming interface works in the following way:
- You can collect data from various sources in Quanos InfoTwin and link it to systems of any kind. To do this, the platform accesses sources such as CRM, ERP, PLM, and content management systems, as well as spare parts catalogs via TwinAPI and transfers the desired data.
- InfoTwin enriches the data and links it in an intelligent and bidirectional manner with applications such as your company apps, your spare parts shop, and service portals. Important: TwinAPI is only able to query information and cannot change it.
- Data networking creates the Digital Information Twin, a digital image of your machines and plants. Quanos InfoTwin also becomes an intelligent, easy-to-use data hub that gives aftersales and service teams access to relevant information from across the entire company.
Why interfaces are set to become even more important in mechanical engineering and machine construction in the future
Efficient interfaces and the integration of service data allow you to make optimum use of data from machines and service processes, eliminate data silos, and develop data-driven business models.
Well-networked machine manufacturers are also able to react more quickly to technological and legal developments, such as the Data Act: This new EU law regulates actions including the exchange and use of machine data in the European Union and will require new data strategies from manufacturers in the future.
It's therefore high time to put your company's data flow and interfaces to the test and take the necessary steps towards digitization. With TwinAPI, you already have a sound technical basis for this today. Find out more about TwinAPI and how you can use Quanos InfoTwin as a data hub: