Best Practice: Digital Spare Parts Catalogs in Agriculture
For manufacturers and operators of agricultural machinery, service is becoming an increasingly important factor. Digital spare parts catalogs offer a simple entry point for both sides. Find out which challenges machine builders can specifically solve with digital spare parts catalogs and how their customers can benefit from them.
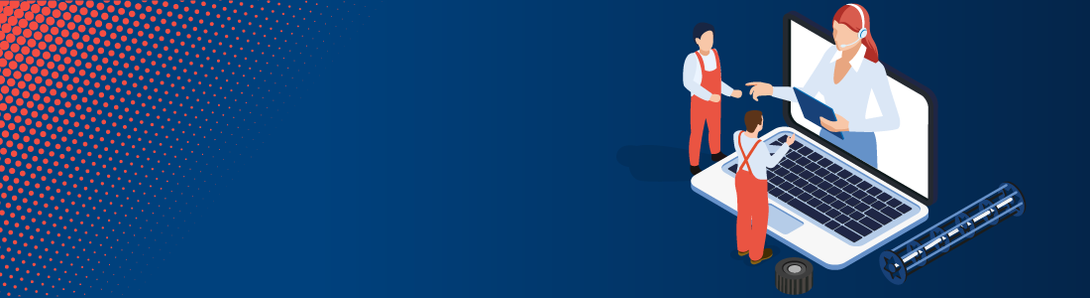
Agribusiness companies have an important task: they supply vital food for the world's growing population. No easy task in view of climate change, harsh conditions in the fields and increasing cost pressure on farms.
Modern agricultural technology supports farmers in their work - but only if combine harvesters and tractors run reliably. This is possible with the support of machine manufacturers and digitization.
The following practical examples show how suppliers of agricultural technology secure their customers' yields with digital tools. To find out what opportunities digitization offers for agriculture in general, read our blog article on the service revolution in agriculture.
Kemper: Improved communication with customers and dealers
Maschinenfabrik Kemper produces harvesting headers and mounted choppers, among other products. The company faced a number of challenges related to spare parts for their agricultural equipment:
- While the customers of the machine factory were already experimenting with satellite-based technology for agricultural vehicles, ordering spare parts for their machines was still done by phone, fax or email.
- For orders, customers used a paper list. This often led to misunderstandings and incorrect orders, because identifying the right parts by their installation position was quite difficult.
- Due to growing competitive pressure, aftersales urgently needed to be realigned.
Kemper decided to launch "Project Future" with an online presence for ordering spare parts. A portal on the Kemper website was to enable dealers and customers to reorder parts for the manufacturer's agricultural machinery around the clock.
Digital spare parts catalogs not only provided the right solution for Kemper's requirements, but also offer other benefits:
- The visual navigation in the online catalog makes it easier to identify the parts customers are looking for.
- With the spare parts catalogs, the manufacturer broke down language barriers in support: 80 percent of the products go abroad via a worldwide partner network and can now be ordered conveniently in the local language of the partners.
- Within a few weeks, Kemper had already implemented a first pilot project. With the existing information on parts lists and an interface to the ERP system, creating spare parts catalogs is possible in no time at all.
Read the detailed case study to find out what other experiences the agricultural machinery supplier has had with digital spare parts catalogs.
CLAAS: Service offering successfully prepared for the future
CLAAS, one of the world's largest agricultural engineering groups, also relies on digital spare parts catalogs in its spare parts business. The company has been paying close attention to the topic of aftersales and service for many years: Spare parts service, customer service and sales go hand in hand.
With this strategy, the company has managed to cover most of its total costs from workshop and spare parts revenues. First, however, some changes were necessary:
- Internal processes related to service had to be optimized and standardized.
- Information from two different spare parts catalog systems for harvesters and tractors had to be merged into one platform.
- Catalog publication, which used to involve a great deal of effort and expense, had to be optimized.
To overcome all these challenges, CLAAS introduced a spare parts information and ordering system based on digital technologies. As a result, the manufacturer is now able to provide dealers and customers with the best possible support when ordering the spare parts they need.
This has been improved by working with digital spare parts catalogs:
- Customers and dealers worldwide use CLAAS' digital spare parts catalogs around the clock as a source of information or an ordering portal.
- All data in the catalogs is machine-specific and available in the users' national language.
- User-friendly search functions simplify the identification and ordering of spare parts. Before the new system was introduced, it was not possible to search for spare parts for harvesters using the serial number. Now, the search via serial number is just one of many navigation options.
- Previously, catalogs were created with an external service provider. Now CLAAS can create catalogs in-house and is independent of third parties.
- The new catalog system is linked to the manufacturer's ERP system - published catalogs can therefore be updated without any effort.
With the new catalog system, CLAAS is able to sell spare parts efficiently and meet customers' increased demands for round-the-clock service and online ordering options.
Read the full case study to find out what other improvements CLAAS has been able to implement in aftersales and service.
Digital spare parts catalogs: a must-have for agricultural businesses
The practical examples show the benefits that digital spare parts catalogs hold for the agricultural industry. In addition to agricultural equipment suppliers, their users also benefit from the service and parts information that modern catalogs provide.
We have compiled further advantages for manufacturers and operators of agricultural technology in an additional blog article.
Farmers get fast help even during the critical harvest season. Thanks to the quick identification of needed parts and the ability to trigger orders themselves, downtime for harvesting equipment operators is reduced. As a result, agricultural machinery operators are confidently able to meet their yield targets. That is not all: digital spare parts catalogs focus on information transfer and the networking of manufacturers and users.
All of this helps to make agricultural technology more transparent and tangible. When farmers use their agricultural equipment and machinery better and longer with more know-how, this ultimately contributes to greater efficiency and sustainability.
Both aspects are important for profitability, but also for the external image of farms and machinery manufacturers. A positive image not only increases the acceptance of modern agriculture, but even helps farmers attract young talent to their farms.
Start your own service revolution now!