Digitization In Mechanical Engineering: How to Steer Your Business Into the Future
Digitalization has revolutionized and simplified large areas of our lives. Modern technologies offer almost unlimited possibilities for this. But many companies do not know how they can now leverage new potential. This blog article shows how machine builders can keep up.
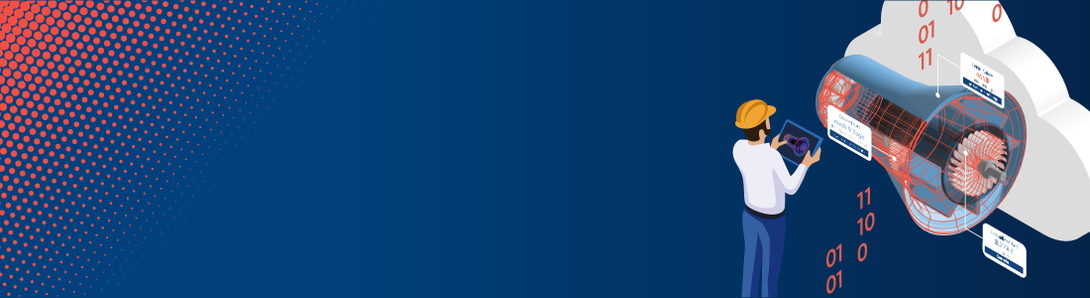
Digitization enables companies to collect information about the operating status and performance of plants in order to optimize processes and avoid downtime. The maintenance of machines and plants can also be optimized by planning maintenance work in advance and reducing the workload of service employees.
Challenges of digitization in mechanical engineering
Those who want to benefit from these advantages must take digitization into their own hands. Otherwise, companies risk falling behind the competition. But as tempting as the benefits of digitized processes are, the hurdles to implementation are equally high.
- One particular challenge in mechanical and plant engineering is protecting production-related data from hacker attacks. Companies must therefore adequately secure their systems and regularly check for security vulnerabilities.
- Another challenge is the integration of new technologies into everyday operations. Without a digital infrastructure and continuous employee training, digitization eats up more time and resources than it could save.
- At the same time, machine builders can only succeed in the competition for customers' attention by introducing new business models.
To remain successful in the long term, companies in the mechanical engineering sector should address overcoming these hurdles rather too early than too late. It's only when this succeeds that digitization in mechanical and plant engineering has the potential to improve plant performance and provide companies with competitive advantages. In addition, digital technologies offer the opportunity to increase customer satisfaction in the long term.
Aftersales as a starting point
An important role is played by the aftersales team, which works closely with customers. Through this exchange, employees gain valuable insights into customers' requirements and needs. With their insights, they make an important contribution to aligning their company's products even better with customer requirements.
At this interface, aftersales is the bridge between customers and the internal processes of machine and plant manufacturers. This department is therefore an ideal starting point for the digitization of corporate processes.
The following overview shows what is possible. You can find more information on the specific areas by clicking on the links that will take you directly to in-depth articles on the Quanos blog.
Networking
A fundamental goal of digitization is to break down data and process silos. It is therefore important to strengthen interfaces and network processes with each other. Two areas in which interaction ensures greater productivity are aftersales and technical documentation.
If existing systems in these areas and the data they generate can be combined, service operations will benefit from greater efficiency.
How can after-sales and technical documentation be connected?
Efficiency tools
Given rising costs and the shortage of skilled workers, companies need more efficiency in their day-to-day work. In aftersales, the networking of knowledge and intuitively usable tools can help to relieve employees and preserve resources. As a result, the team has more time to attend to customer concerns and to develop and implement new services.
Self-Service
Many industrial customers are used to placing orders in online stores by themselves from their private lives. In the B2B sector, too, customers like to take control when it comes to selecting and ordering spare parts, for example.
An important trend in mechanical and plant engineering is therefore the development of digital self-services. Companies use online portals to give their customers easy access to information from maintenance and operating manuals or other elements of technical documentation.
Cloud platform
An important issue related to digitization is infrastructure. The modern business world is moving faster than ever before. That is why more and more machine and plant builders are choosing the cloud instead of on-premise solutions.
This makes them more flexible in implementing digitization and they can already achieve a lot with manageable investments. It also allows them to lay the foundations for flexible digital services and connect existing tools more easily.
An easy entry into digitization: The Quanos InfoTwin
Quanos InfoTwin offers a particularly convenient way for machine and plant manufacturers to digitize their after-sales processes. With the help of this cloud platform, information from aftersales & service can be intelligently networked.
Whether as a starting point for smart services or as a basis for digital twins: Quanos InfoTwin combines all the advantages of modern cloud solutions in one system that can be seamlessly integrated into the existing tool landscape.
The platform offers a convenient entry into digitization and overcomes several challenges at the same time:
- High data security protects production data
- Intuitive operation leads to minimal training requirements
- Modern cloud platform reduces investment in infrastructure
- Rapid entry into digitization secures competitive advantages
The know-how from over 1,000 customer projects in mechanical and plant engineering has flowed into the Quanos InfoTwin. See for yourself today how compatible it is with your processes and test the Quanos InfoTwin free of charge - so that digitization is not a threat but an opportunity for your company.
Other articles from Quanos
This might also interest you
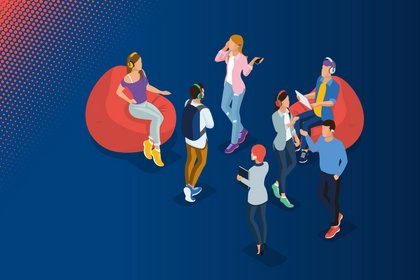
„Doku-Lounge“: Auf dem roten Sofa mit Kerstin Berke und Philipp Eng
Moderatorin Kerstin Berke und Marketingspezialist Philipp Eng sind das Duo vor und hinter dem Mikro der „Doku-Lounge“…